Loading Guide - Friction
Loading Guide - Friction
National
Heavy
Vehicle
Regulator
This guide is part of a series of loading guides that provide tips and tricks to help you understand good load restraint. More detailed information on the principles covered by this guide and comparing the load restraint friction force between two surfaces can be found on page 243 of the Load Restraint Guide 2025.
What is Friction?
Friction is the force that makes it difficult for one object to slide along the surface of another.
For example, you might have noticed that it is difficult to push a box along a cement floor. This is because friction acts between the surface of the box and the surface of the floor.
In load restraint, there are two types of friction:
- static
- dynamic.
Static friction applies before load movement begins. Dynamic friction applies once the load movement has commenced.
The Load Restraint Guide case studies and tables are based on static friction.
Why is Friction important?
Friction is important because it helps to restrain the load.
When using the tie-down restraint method, friction contributes to stopping the load from moving forwards, sideways or backwards. Increasing friction can reduce the number of lashings required to restrain a load, this improves efficiency without compromising safety.
How is friction used to help restrain my load?
Increasing the friction between the load and the deck of the vehicle makes it harder for the load to move.
Friction is generated from both the weight of the load and the clamping force applied by the tie-down lashings.
For tie-down restraint to be effective, the load must be in contact with the vehicle throughout its journey.
The weight of the load alone does not provide adequate friction to restrain it.
Using the tie-down method to increase friction
Friction can be increased by adding tensioned lashings over the load.
These lashing effectively pull the load down to the deck of the vehicle.
The higher the angle of the lashing the more clamping force is applied. One lashing at 90° generates the same clamping force as 4 lashings at 15°. The ability of the lashing/ratchet to provide pre-tension also effects the clamping force.
Using high pre-tension lashings/ratchets can reduce the number of lashings required.
Example | Approximate angle | Tie-down angle effect | Tie-down effectiveness |
---|---|---|---|
![]() |
90° | 1.00 | 100% |
![]() |
60° | 0.85 | 85% |
![]() |
45° | 0.70 | 70% |
![]() |
30° | 0.50 | 50% |
![]() |
15° | 0.25 | 25% |
Tips
A simple method of testing friction is to place an object on a surface and tilt that surface until the object begins to move.
On a surface with low friction the object will move at a lower angle compared to the medium friction and the object on the high friction surface will resist moving at even higher angles
Friction can be increased by adding lashings and clamping the load down.
4 x lashing at 15°, is the same as 1 x lashing at 90°.
A high pre-tension ratchet will produce higher clamping forces than a standard ratchet.
Risks
When designing a load restraint system consideration must be given not only to the friction between the load and the deck of the vehicle but also between any layers.
With bundled products, sometimes clamping is not enough to restrain the entire load. Consider belly wrapping or using a structure at the front and back to prevent the movement of product within the bundle.
Steel tracked equipment such as an excavator has very low friction when placed on a steel deck, in this instance direct restraint is considered the appropriate method for effective restraint.
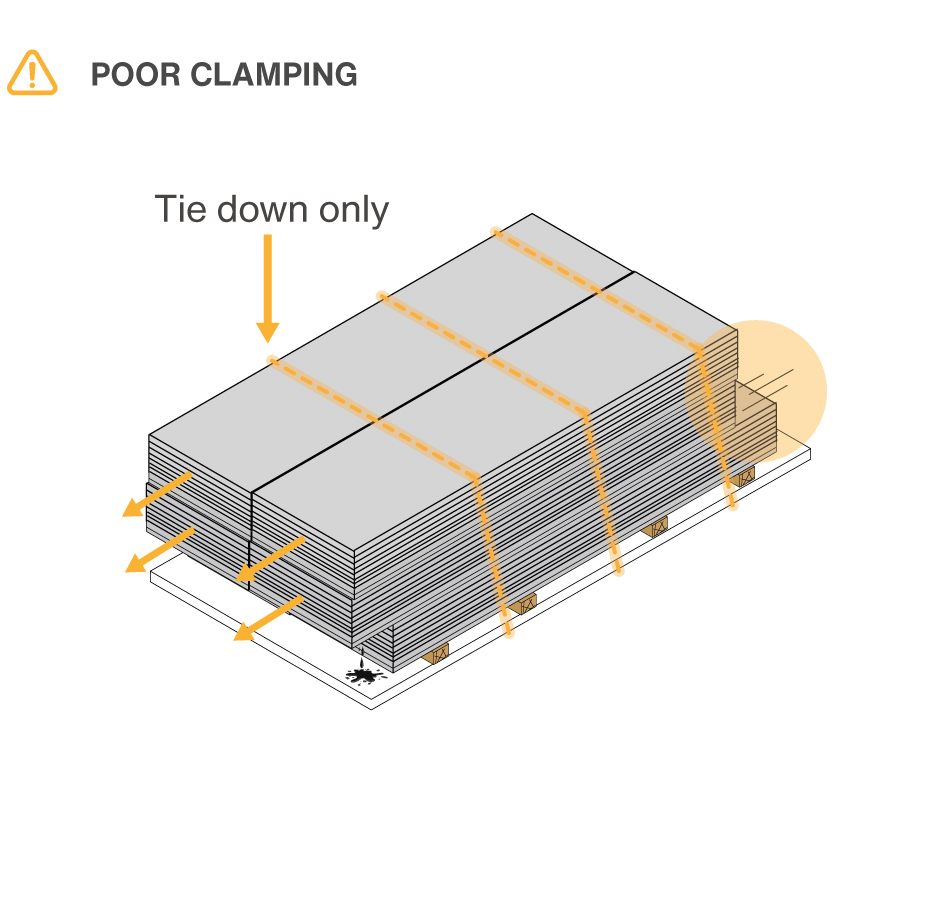
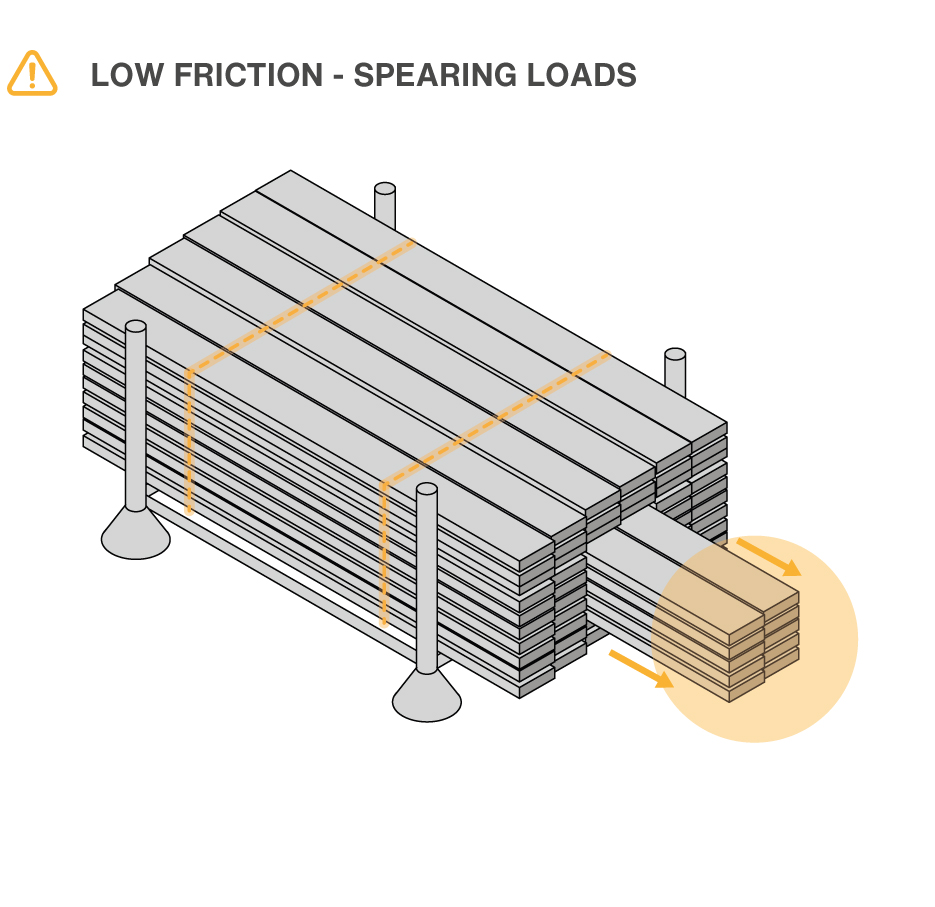
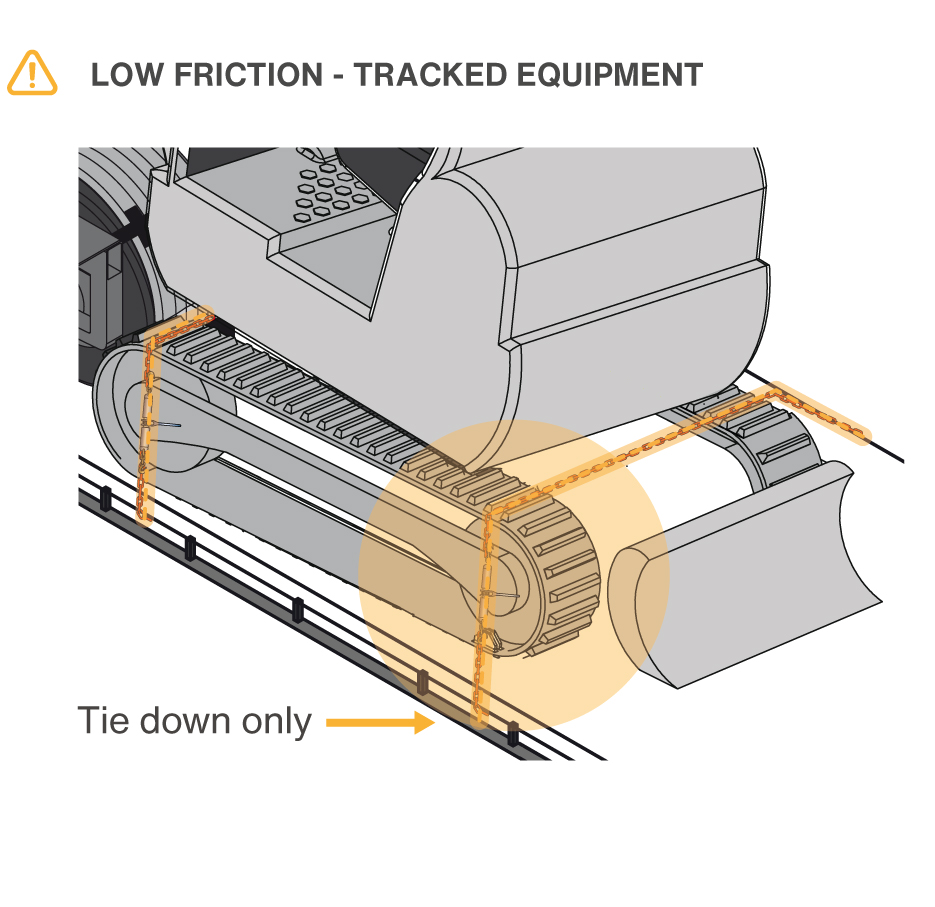
Good practice
Using dunnage with high friction rubber load mat on either side will increase the friction between the load and the deck of the vehicle.
Intermediate Bulk Container (IBC’s) often have a metal frame and placing timber or rubber under the frame will increase friction.
You can also place higher friction material between layers of the load to increase friction and control the movement.
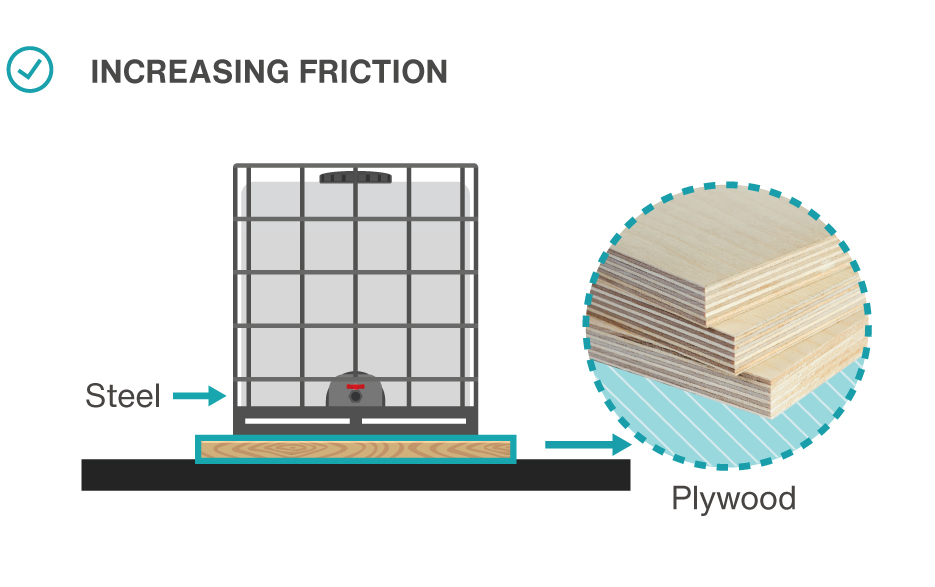
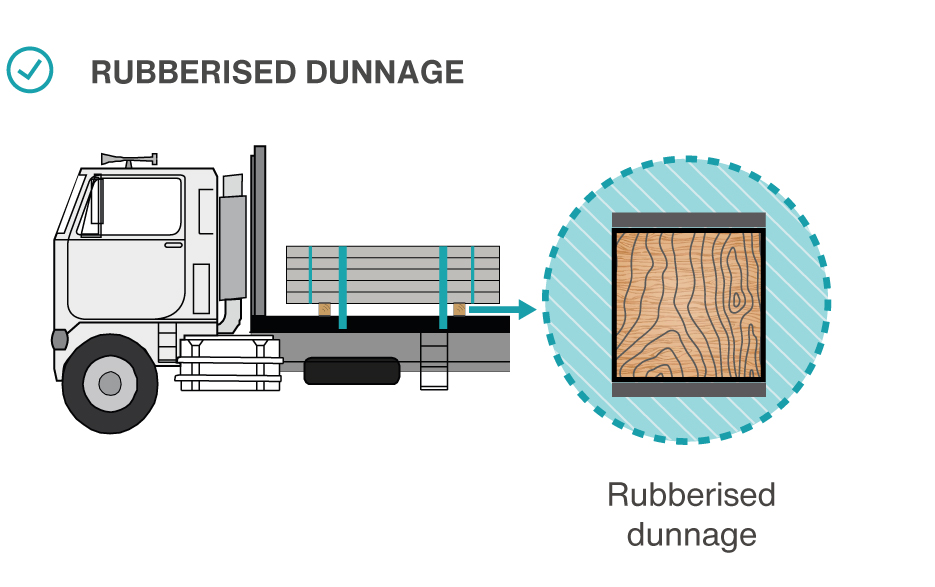
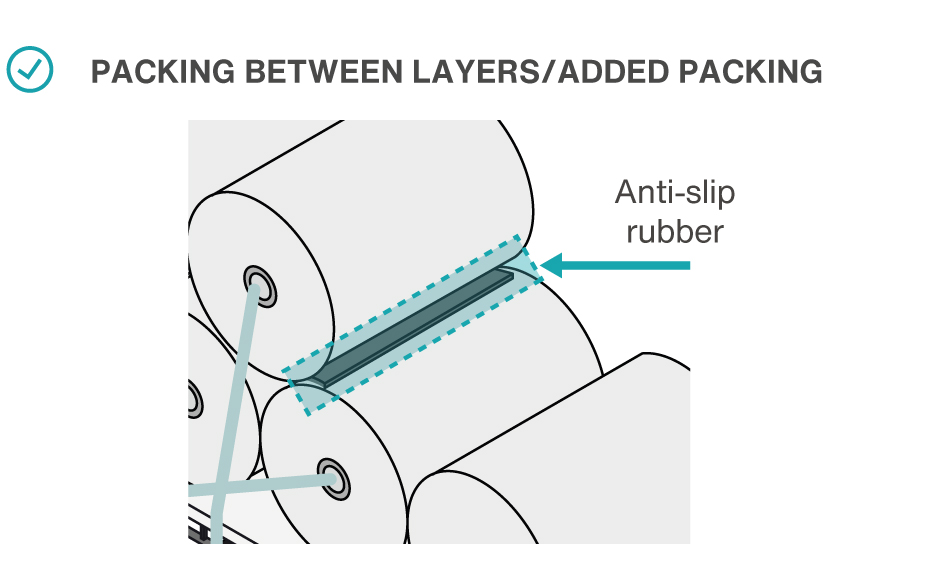
Case study
A heavy vehicle was stopped carrying an 8,000kg sandstone block in a metropolitan area.
The block was sitting on timber dunnage with two lashings that have a pre-tension of 750kgf each.
If you look at the table on page 271 of the Load Restraint Guide 2025, for a load that is not blocked against the headboard, you will see with medium friction (timber 0.4µ) and two lashing at 75°, the load restraint system is capable of 2,800kg. Well below the required 8,000kg.
If you were to add high friction rubber matting between the deck and the timber dunnage and also between the timber dunnage and the load (sandwich the timber dunnage), the system is capable of 8,600kg.
By using the tables in the load restraint guide, you can demonstrate that you have met the Loading Performance Standards.