Step 1 - Introduction to SMS
Having a Safety Management System (SMS) can be one of the most effective ways to meet your safety obligations under the Chain of Responsibility (CoR) and the Heavy Vehicle National Law (HVNL).
The 9 Step SMS Roadmap is designed to guide the adoption, development and implementation of an SMS as part of your day to day business. Each step contains an important function or element of an effective SMS. Whether you are "Starting Out", "Improving On", or aiming for "Continuous Improvement" on your SMS journey, having each of these elements in place can greatly assist you with managing safety risks in the business.
The 9 Steps describe an optimal roadmap to developing an SMS, filling the gaps in an existing SMS, or improving the performance of an already implemented system. NHVR’s recommended approach is to choose where you believe your system is at now, and progress through the steps in order – from 1 through to 9. By using the 9 Step SMS Roadmap you agree to the following terms of use.
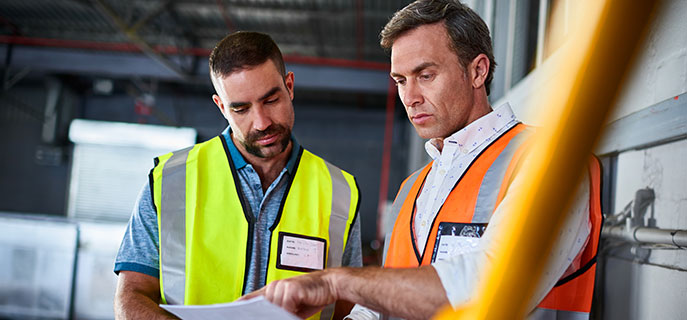
In each Step, the "Starting Out" journey contains information for the business where none, or very few, documented SMS elements or functions are in place. This is a good place to start for those new to or unfamiliar with implementing an SMS as it contains guidance on the key system elements and foundations.
"Starting Out" focuses on providing your business with the foundational SMS elements for development and implementation. Upon completion, you should then move through each of the 9 steps again under "Improving On" where there is a focus on other key SMS elements and processes. Before going to step 2, read the SMS Fact Sheet. It overviews how an effective SMS can be beneficial in managing the safety risks of heavy vehicle operations and transport activities. You should also determine what SMS elements you may yet require as part of your business, utilising this Safety Management Systems (SMS) Checklist.
The "Improving On" journey provides guidance for you to build on an incomplete or newly developed SMS. It contains information on how to develop those elements that are still missing from and required for your SMS. Development of these will further complement your existing SMS processes making the system far stronger and more effective.
Before going to step 2, read the Introduction to SMS in the Heavy Vehicle Industry. It provides a more detailed overview of all key elements you should develop in your SMS, why each is important and how they collectively deliver effective safety outcomes when implemented.
The "Continuous Improvement" journey describes how an SMS that is already documented and in place, can be made more effective and meet the changing needs of the business.
This journey provides guidance aimed at bridging the gap between a documented SMS and employees needing to better understand and embrace the system’s key functions and requirements. Targeted toolbox talks, safety briefings and safety committee meetings are all excellent tools to help management and employees deliver on an effective SMS, both corporately and at the depot or shop floor.
Once in place and functioning, an SMS also requires regular review to identify where it can be improved upon or made more effective. This helps to ensure the SMS is fit-for-purpose and can be used effectively to improve the safety of your heavy vehicle operations and transport activities.
Whilst effective safety outcomes are the primary focus of implementing an SMS, it can also help a business meet its Safety Duty, Chain of Responsibility (CoR) and other obligations under the HVNL. Answering each part of the CoR Gap Assessment Tool will help identify where you may be able to further improve your system to improve safety and compliance.
Step 2 - Risk assessment, treatment and monitoring
The heart of every good SMS is an effective approach to managing safety risks. This includes being able to identify those risks, consider how they could impact your business, what risk controls are in place, if further treatments are required, and monitoring to ensure all is working as designed.
Common risk management tools such as risk assessments and risk registers are used in all types of businesses around the world, as the cornerstone of their SMS. Embracing their development, implementation and regular review is critical for your SMS journey; whether your SMS is just "Starting Out", requires "Improving On" or needs "Continuous Improvement".
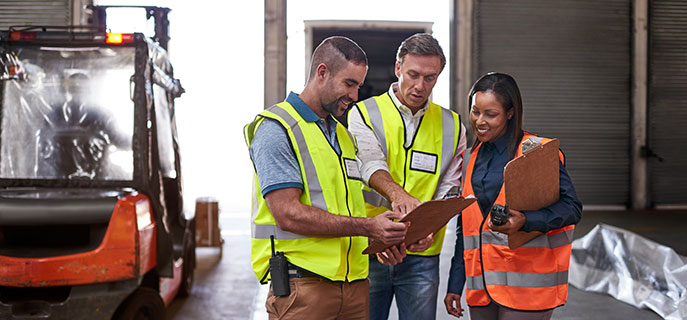
Starting out a journey for good risk management doesn’t need to be difficult. Sometimes it is just a matter of better understanding and documenting the safety risks you know are already in your business and what controls are in place to help manage them; even if those controls are yet to be formalised or documented.
You should first look at developing a safety Risk Register for your business. Completing and updating a risk register enables you to keep an up-to-date understanding of the risks in the business and identify whether enough is being done to manage those risks.
The Risk Register - Quick Guide describes a step by step process to identify and assess safety risks and their potential for harm, how the risks are controlled, what additional controls might be needed and how to ensure the controls are working.
You can use or adjust the Risk Register - Template as part of your own SMS and populate it with your business’ key risk management information. The template identifies commonly accepted heavy vehicle safety hazards – such as fatigue, speed, mass, dimension, loading or vehicle standards. The template can be adjusted to document whatever safety hazards and risks are apparent in your business.
To assist you further, a worked example of a Risk Register, utilising the Risk Register - Template has been developed. It is a useful reference that demonstrates the different types of risk controls and methods to review the controls.
Once you have a documented and functioning risk register in place, you can take the next step in improving the control and management of risks in your business. Whilst a risk register summarises all your risks and controls in the one document, more detailed assessments of each major risk will help enable more effective management.
Undertaking a risk assessment of each safety risk provides greater detail around the possible adverse impacts to an individual, the business or the community should that risk be realised (for example, if a driver crashed a truck after leaving a depot in a fatigued state). It also helps better determine every control in place and if further controls or treatments are necessary.
Individual risk assessments are also beneficial in pulling together affected supervisors, managers, and staff in a timely manner to gain their views and support on the outlined risk controls and treatments. Chapter 3 of the registered Master Industry Code of Practice for heavy vehicles also explains in detail the accepted industry standard for identifying and assessing safety risk.
You can utilise the Risk Assessment – Template in your own business as part of an SMS. The template includes a series of prompts and questions to help populate it with relevant risk and control information. The Risk Assessment - Worked Example utilising the template is a useful reference around how a typical populated risk assessment may look.
Once you have developed risk assessments for each of your identified heavy vehicle safety risks, ensure you circle back to your higher-level Risk Register and update it with any related changes; such as any new or amended risk controls and treatments.
Like other important processes within your business, periodic reviews of your populated risk register and risk assessments help ensure you and your staff are refamiliarised with their content and put in place any required amendments and changes. Aim to formally review your risk register and risk assessments at least annually to keep them update to date and effective.
To continually improve your risk management, it is also important that staff understand their own role in identifying and managing relevant safety risks. Direct encouragement and education can be undertaken via short, targeted discussions with staff by their supervisor or manager. The Heavy Vehicle Safety Risk and Controls in my workplace – Toolbox Talk is an example of how staff can be briefed on how your business undertakes safety risk management, why its important for their safety and wellbeing, and how they can become involved in contributing to the wider process.
Companies with an effective SMS in place will choose to print an enlarged copy of their populated risk register and post it on the wall of depots, meal rooms or other areas where staff congregate and are able to stop and read it. This often generates questions and comments from staff, raising safety culture and contributions to safety improvements.
Step 3 - Hazard and incident reporting
A hazard and incident reporting process is integral to an effective SMS. Put simply, it helps identify where things could go or have gone wrong and a concerning safety issue has or may arise. The reporting and subsequent identification of safety hazards and incidents in your business helps continually inform a range of other vital SMS components. These include risk assessments and risk registers, incident investigations, and continuous improvement. Most importantly, it is the initial timely process that helps determine steps to prevent safety incidents reoccurring.
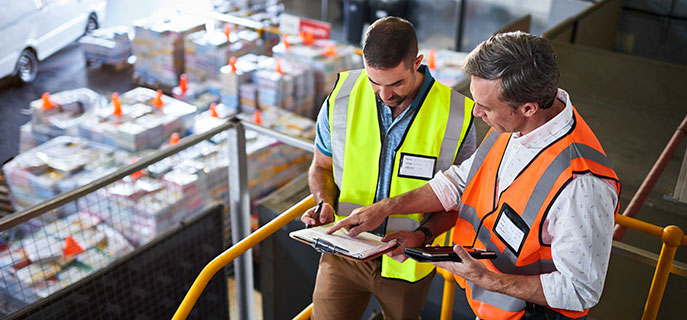
Developing an Incident Reporting process that can be easily understood and utilised by all staff is a great first step for this component of your SMS. It allows seamless staff involvement, and the business can be made aware of incidents, including ‘near miss’ events in a very timely fashion. Recorded incident details can also be utilised at a later stage if required, for a safety investigation to identify the incident causes and areas for improvement.
The Incident Reporting - Quick Guide describes the type of information staff and managers should be encouraged to report, such as who was involved, what task was being done, where and when the incident happened and any other information about the event.
You can utilise or modify the Incident Report Form - Template within your own SMS to record safety incidents and possible treatment options.
The Incident Report - Worked Example utilising the template is a useful reference around how a typical populated report may look.
Focus on developing and implementing your formal approach to reporting safety incidents, including regular education and reinforcement to all staff over a period of time. This helps cement a positive reporting culture between staff and management and provides a great avenue for employees to be actively involved in improving safety within the business.
Consider focussing on Hazard Reporting to improve on your suite of SMS tools after you are confident Incident Reporting is working as you expect in the business.
Once Incident Reporting processes are formalised within the business and are being embraced and utilised by all staff and managers, you should expand your SMS to include Hazard Reporting.
Hazard Reporting enables the business to assess the risks - such as a driver crashing a truck, of identified heavy vehicle safety hazards – such as a fatigued driver, and to develop controls or further treatments to help mitigate those risks – such as appropriate driver rostering.
You will recognise that identifying and better understanding where those hazards exist as part of your business, feeds directly into the risk management components of your SMS. Staff and managers are a great resource within the business to help with the identification process, provided there is some form of Hazard Reporting mechanism in place.
The Hazard Reporting - Quick Guide describes how staff and others can easily identify and report to management where they believe your heavy vehicle transport hazards exist.
You can easily adopt and utilise the Hazard Report Form - Template within your own SMS. Encouraging staff to utilise this will not only help identify hazards that inform the wider risk management process but demonstrates you also value the views and involvement of employees in improving safety outcomes and culture.
Documented hazard and incident reporting processes within an SMS will not be effective unless staff and management actively embrace and utilise them. To drive a good reporting culture – critical in continuously improving your safety management and performance, staff must be actively encouraged to use those systemic processes and management must follow-up and provide feedback on reported incidents and hazards.
The Reporting Safety Hazards and Incidents – Toolbox Talk is an excellent way for managers and supervisors to locally discuss with staff how incidents and hazards are reported internally, why it is important, and reinforce that management will not penalise but actually encourage reporting.
Your business should also consider providing similar advice and hazard and incident reporting requirements if necessary, to third parties that you engage to undertake heavy vehicle transport activities for you.
The Risk Management - Identify Hazards Video can also be presented to managers and staff. It highlights the importance of hazard and incident reporting including how it can have a positive impact on safety outcomes and performance.
Step 4 - Management commitment and documentation
A visible and demonstrated commitment to safety by management always underpins an effective SMS and positive safety culture. It illustrates to all staff, customers and third parties how seriously safety is taken by your business and should be reflected in the way the organisation operates on a day-to-day basis.
Whilst most parties in the heavy vehicle Chain of Responsibility take safety seriously and have good safety risk controls in place, many companies do not take the extra step of actually documenting them.
All key functions of your SMS, including key risk controls, should be documented to help lock in and reinforce critical safety processes, to educate and train staff, formally record incidents and other safety information, assist the executive in meeting their HVNL due diligence requirements, and should it be required – help demonstrate that you are effectively managing your heavy vehicle safety risks, so far as is reasonably practicable.
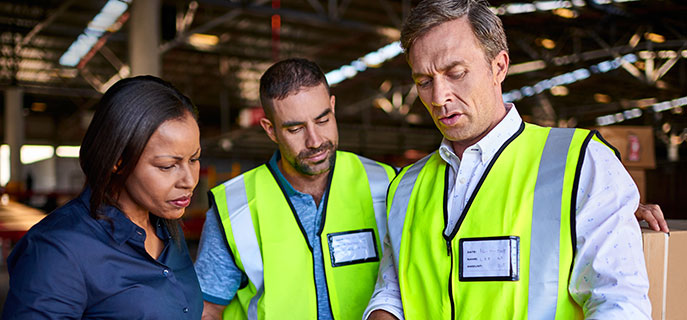
Developing a Safety Policy is a good way to demonstrate and explain the importance and commitment that management places on safety for employees and others that interact with the business.
The Management Commitment and Responsibilities - Quick Guide provides information on what you should consider including in a safety policy. It describes how to set clear direction from management around its commitment to safety and what it will do to help fulfil that commitment. It also describes the importance of defining the roles and responsibilities for managing safety risks, and how to best engage and empower employees who are often tasked with implementing safety critical tasks.
You can utilise and adapt the Safety Policy and Responsibilities - Template within your own SMS. It sets out a wide choice of safety policy aspects that management could commit to, along with a choice of probable or potential safety responsibilities for executives, management, employees and third parties, dependent on the size, complexity, and nature of your business. You can just delete, add to, or modify the policy and responsibility points within the template to suit. The Safety Policy and Responsibilities - Worked example utilises the template and shows what a safety policy could look like.
At this point of your journey, you should primarily focus on formally documenting the key products recommended to be developed and populated so far (such as a Risk Register, an Incident Reporting form, or a Safety Policy) and any other products suggested in the remaining "Starting Out" steps. Don’t be afraid to copy and utilise any of the provided templates within the 9 Step SMS Roadmap and adapt them to suit your own business if desired.
Regardless of the size or complexity of a business, it is important to have a visible Safety Policy and formally documented responsibilities that are communicated and understood across the business.
Consider printing and framing the organisation’s Safety Policy and placing it in several prominent positions in the workplace. This demonstrates to staff and third parties that safety is a high priority within the business, with management committed to it via provision of resourcing, training, systems, and equipment.
Once you have documented and populated all of the SMS products recommended within the 9 Step SMS Roadmap so far (such as Risk Assessments and Hazard Reporting forms), it is important to progress formalisation of your safety risk controls.
Documented procedures that explain the safety process and related risk controls in more detail support employees in meeting their safety responsibilities when performing specific tasks. These procedures help reduce the likelihood of safety incidents occurring by documenting how specific tasks can be performed safely in a step-by-step fashion. They are also vital in helping train and educate new staff to correctly perform those tasks.
The Developing Procedures - Quick Guide describes the best way to document a safety task and what should be included within a procedure.
A good way to start developing a procedure is to work with staff to write down the steps that are already being performed to complete a task. Including images in a documented procedure may also be useful to help staff understand key steps. Check the procedure by observing employees undertaking the task to ensure that all the steps are included and are followed.
It is important that the procedure describes the purpose of the steps and how they control the safety risks. Make sure that employees know where to find the relevant procedures for their tasks, are trained in the procedure, and have the competency to perform the steps.
You can utilise the Procedures - Template to document any number of procedures within your own business, as part of your wider SMS.
SMS related procedures can come in all sizes and complexity however this Procedures - Worked example utilising the template provides a useful reference if required.
Whether you have recently developed a Safety Policy or plan to review the current version, genuinely engaging staff in the process really demonstrates to them that management is interested in their views and opinions, particularly in keeping them safe. Ensure your review processes brings staff or their representatives on early allowing them time to seek colleagues’ feedback where needed.
You should also regularly raise your Safety Policy and Responsibilities document (and its important contents and intent) with staff. This again helps reinforce management commitment and sets a safe platform for staff to raise safety issues or possible improvement solutions. The Our Safety Policy - Toolbox Talk is an easy mechanism for managers and supervisors to use to discuss the Safety Policy in this way.
Once you believe you have formally documented all of your SMS procedures, forms, templates, and other products, consider combining them all safely in an easy to access SMS Manual. This will ensure that all documents are in a single place, either in hard copy or electronically. Most importantly, you want your SMS, or vital components at least to be accessible for easy use by staff. Seeking regular feedback from staff on how user-friendly they think different documented components of the SMS are will also provide valuable feedback on the system’s usability.
Step 5 - Internal safety investigations
Once a business has a working Incident Reporting process in place, the next logical step for your SMS is enabling you to investigate safety incidents.
Investigating reported incidents helps establish how and why it occurred. This helps reduce the likelihood of similar events recurring by identifying the causes and contributing factors and exploring opportunities for safety improvements.
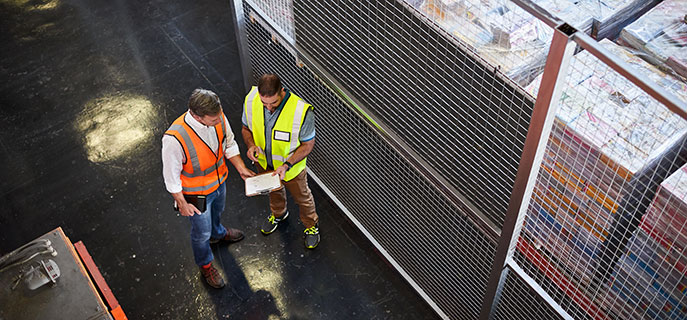
When initially building an SMS, your main focus for investigating safety incidents is twofold.
Firstly, once the incident is reported, reinforce with staff that there is to be no apportioned blame. You may have already stated as much within your Safety Policy. Communicate to staff that the organisation just wants to understand what caused the event and what it can do to help prevent it from happening again.
Secondly, because you are still building your SMS capability, undertake a simple shopfloor investigation into the incident. This involves stopping work at the depot or workplace for a short period - say half an hour to an hour. Then with the affected staff members or team and their supervisor/manager, have an informal and open discussion about what they think caused the incident; it’s important not to direct blame at anyone. Once the group agrees generally on what caused the event and what the team or business should do to prevent it happening again, record those action details. You can utilise this Continuous Improvement Register - Template (DOCX, 44KB) to record any improvement action details including who will undertake them and when they will be completed by.
Should an incident occur that results in a serious injury to staff or others, and you don’t yet have the systems or capability to investigate it within the business, consider engaging a specialist investigator to undertake the task. They will generally utilise and follow well recognised professional safety investigation systems and methodologies to help you determine what caused the serious incident.
As your documented SMS and its implementation matures, so too will your organisation’s capability to undertake more complex safety related tasks. With some simple systemic guidance, templates, examples and practice, most managers or supervisors will be able to undertake more comprehensive safety investigations. This capability can also be supplemented by commercially available safety incident investigation training.
A good starting point for managers or those looking to increase their investigation capability is to utilise the Incident Investigation - Quick Guide. It provides useful and structured guidance in developing and undertaking a safety investigation and related processes.
A timely and structured process will help someone conducting the investigation to build a complete picture of how and why an incident occurred. Working with staff involved in the safety incident also assists in more formally reconstructing the event and gathering the information for the investigation and report.
You may want to consider adopting the Incident Investigation Report - Template within your own organisation’s SMS to record the information collected as part of investigating an incident and to analyse the risk controls that were in place.
This Incident Investigation Report - Worked example illustrates the type of information that an investigation may record, including key risks controls, related findings and required improvement actions.
Investigating a concerning safety incident should not just be the role of a manager or supervisor. Including affected staff member/s often provides more rounded input to an investigation with a range of contributing viewpoints. Involving staff in the investigation also helps reinforce that your organisation does not apportion blame when safety is involved.
You should consider managers and supervisors utilising the Safety Investigations – Toolbox Talk with staff at regular intervals, depending on the size of your business. It reinforces why reported safety incidents need to be investigated, how an investigation is conducted, how staff can be involved, and progressing any improvement activities.
Finally, consider how an investigation’s outcomes can be communicated to all staff including agreed improvement processes. Consider whether these safety communications should also be given to external parties including sub-contractors and customers.
Step 6 - Safety training and communication
Almost every business in some way provides education, advice, or training to staff to help ensure they remain safe at work, and don’t contribute to causing some form of safety incident. Having a greater and more planned focus on the critical safety training requirements in your business will further strengthen and complement the controls in place to reduce the impact of your heavy vehicle safety risks.
Planned and structured communications to staff about the organisation’s SMS, its key components, and the safety role of management and staff will result in greater workplace engagement and system effectiveness.
Targeted and scheduled safety training and communication are important practices that can assist you in developing and supporting a positive safety culture and sustaining safety in the business.
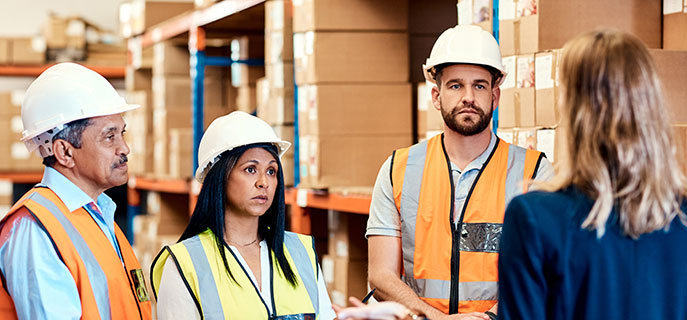
Training and communication involves sharing information that explains the importance of safety and how safety risks can be managed through appropriate skills, behaviour and knowledge.
In "Starting Out" your SMS journey, focus on discussing with managers and supervisors what they believe is the key safety training that staff will require over a 12-month period. The risk controls identified within your populated Risk Register will help inform those considerations – such as training drivers around fatigue management or training staff to effectively restrain vehicle loads.
You can utilise this simple Safety Training Calendar - Template as part of your own SMS to record each staff members’ or teams required and completed safety training.
It’s also good to communicate directly with staff the importance of having an SMS in place and how they can contribute. Familiarise yourself and management with the principles and recommended approaches in the SMS Awareness Training - Quick Guide.
The Safety Promotion and Communication - Quick Guide also provides detailed examples on the various ways you can promote safety practices within the business. You can consider them all or just a few, depending on the size and complexity of your business. It also contains a checklist to help you determine the most effective safety communication methods for your organisation.
Safety training and communication can directly help improve safety performance by communicating lessons learned, safety principles and broader safety information.
It may also be used to support staff in understanding business policies, procedures, and processes, by providing a focus on safety efforts and how seriously safety is taken. Providing training and communication can be as simple as speaking to staff, such as through toolbox talks, or may be formalised through a training program.
The How to Run a Toolbox Talk - Quick Guide provides information, hints and tips on preparing, delivering and recording the safety information being provided to staff.
This structured Toolbox Talk and Attendance Form - Template can be adapted and utilised as part of your own SMS. The template can be populated and used to keep staff informed and up to date about safety matters in the business. It also provides a shop floor method to keep a simple record of where and when specific safety advice, education, training, communication, or support has been provided to staff.
The NHVR has developed several populated toolbox talks as part of the 9 Step SMS Roadmap guidance to industry. The Safety Training – Toolbox Talk is a good example of how you may populate your own, using the Toolbox Talk and Attendance Form - Template.
There are times when an important safety message or communication needs to be promoted to staff in an urgent or timely manner. Such communications, which may also be required to be delivered to your engaged third parties, can often follow a significant or concerning safety incident within the business. An investigation of the incident could lead to the need for amended risk controls in the workplace with those changes communicated via a Safety Alert. You can utilise this Safety Alerts - Template (DOCX, 154KB) within your own SMS, particularly to communicate the need quickly or urgently for new safety actions to be put in place.
The Safety Bulletins - Template (DOCX, 148KB) is also a useful addition to your SMS to deliver more general safety messages via a documented process. Whilst sometimes not as effective as face-to-face toolbox talks or briefings, Safety Alerts and Safety Bulletins are both relatively simple and positive ways to communicate more widely in the business and to other third parties.
In a mature SMS, planned, positive and targeted safety promotion can be the difference between having an effective SMS and having an SMS manual that just sits on a shelf.
Effective training and communication require the involvement of all staff to share attitudes, values, and beliefs to influence a positive safety culture.
The Positive Safety Culture - Quick Guide provides advice around a more proactive approach to developing a positive safety culture including ways to encourage staff involvement. The described components of a positive safety culture include building a culture of trust, being informed, embedded behaviour of reporting hazards, risk, incidents, near misses and safety concerns, as well as a willingness to learn and change.
Step 7 - Safety performance monitoring
Safety performance monitoring helps to measure the quality of safety practices in your business to meet any established safety objectives.
Establishing safety objectives can help to:
- understand if your SMS is doing what it is intended to do
- identify areas that aren’t working well
- make adjustments to improve the SMS.
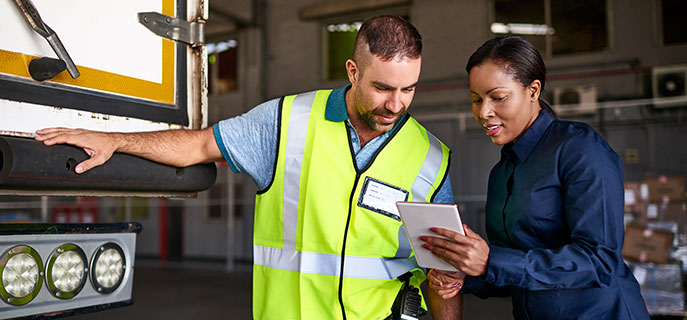
At this stage of your journey, you should concentrate on determining if the platform components of your SMS (such as the ones already described in Steps 1-6) are now genuinely developed, populated, and being implemented.
Performance monitoring now can entail simply checking with managers and staff that your already developed SMS processes and products (such as a populated Risk Register or documented safety procedures) are well known and understood, accessible by all staff and are actually being used by employees as designed.
Should you determine that some of your SMS processes are still not working as designed, reconnect with the management team and staff representatives. Together you can reconsider new or amended plans of attack for the affected areas, utilising tactics such as further education, training and promotion, simpler more user-friendly documents or guidance, and targeted communications.
Consider recording any improvement actions that arise from your performance monitoring within the Continuous Improvement Register - Template. This provides a formal record of your planned improvements actions, who will lead them and when they need to be completed by.
At this stage of your SMS journey, you should consider developing simple, easy to understand safety objectives for your business. Formalising these helps focus your safety performance monitoring, especially if the objectives are easily measurable and well structured.
A common approach to developing safety objectives within an organisation is to utilise the SMART principle. This helps ensure your objectives are:
- S – Specific: more specific the objective, the more chance of achieving it
- M – Measurable: identify the data used to measure performance
- A – Attainable: set realistic objectives
- R – Relevant: focus on improving safety in the business and transport activities
- T – Timely: commit to a timeframe to meet the objective
The SMART principle is described in detail in the Safety Performance Monitoring and Measurement - Quick Guide. It also provides several examples of safety objectives for heavy vehicle transport activities; such as All the heavy vehicles in our fleet will be maintained in accordance with the manufacturer’s maintenance schedules.
It is a good time now to circle back to your developed Safety Policy (where you may have used the Safety Policy and Responsibilities - Template) and update it with your new or amended safety objectives. Once safety objectives have been established, it is important to monitor and evaluate achievements in meeting the objectives. Monitoring and reporting on safety performance has benefits that include:
- demonstrating that the business takes safety seriously
- demonstrating to staff and external stakeholders that the business provides a safe working environment
- providing managers with safety intelligence so they can make informed decisions.
Regular reporting on safety performance can capture progress in meeting your safety objectives.
Consider using information from your safety assurance activities (such as investigating incidents or auditing the effectiveness of documented risk controls) to monitor and measure the achievements against safety objectives. For example, the risk register, incident reports and safety investigations may contain valuable safety information and trends when gathered over a longer term. This information may help you in determining whether safety objectives have been met.
Remember to formally capture and document any resultant improvement actions and communicate them to staff and affected third parties.
Consider also, adopting the Testing the effectiveness of Risk Controls – Toolbox Talk as part of your own SMS. It is useful for managers and supervisors to tell staff why the business monitors the performance of its safety processes and objectives, how staff can be involved and contribute, and to reinforce the process is all about improving safety and not catching people out.
Step 8 - Third party interactions
Transport activities often involve interactions with third parties who have a shared responsibility for the safe use of a heavy vehicle on a road.
A third party interaction exists where an external party can influence or control the safety of transport activities of your business, even if there isn’t a formal agreement in place with the third party. Examples of third parties include you working for clients, sub-contractors working for you, or maintenance and equipment service providers.
When third parties interact, new risks may arise that are beyond the scope of their existing SMS.
Documenting third party interactions as an integrated component of your SMS helps the business to identify, understand and manage the shared safety responsibilities for heavy vehicle operations.
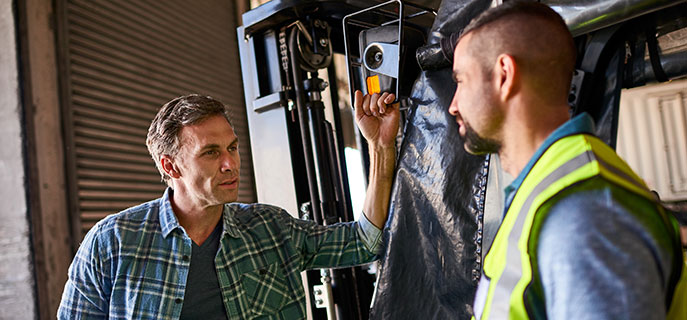
A good starting point to effectively managing third party interactions is to identify the roles and responsibilities that they (third parties) have in relation to safety. This can also highlight the safety responsibilities of the business or identify safety risks to the third party.
The level of responsibility that each business or person has depends on their ability to influence, control, and make decisions relating to the transport activity.
By identifying these roles and responsibilities, it can help the business and the third party understand each of their safety duty requirements under the Heavy Vehicle National Law. Developing a simple spider diagram with your business in the centre and drawing the linkages to your third parties often helps understand which group or business may have the most direct or indirect impact on your safety.
After understanding which third parties’ activities present the highest safety risk to your own business and activities, you should then seek to best understand the procedures and processes that the groups utilise themselves. For example, if a third party in conjunction with your driver loads your truck at a depot, you should be aware of and satisfied with the loading role of the third party.
A good business practice is to share the safety critical procedure or checklist that your staff utilise, with the third party that is involved in that activity. You and the third party organisation should then be in a good position to be satisfied (or not) with the shared roles and responsibilities of each other. If not, then changes to the procedure should reflect the required needs along with any formal changes to contractual requirements between parties if needed.
Reviewing the safety of transport interactions with third parties is important.
The Third Party Interactions - Quick Guide describes in more detail how you can undertake such reviews as well as explaining the key safety duty requirements of all parties in the Chain of Responsibility under the law. Importantly, it also provides practical guidance for documenting third party interactions.
Working collaboratively with other third parties involved in the transport activity will help identify and address gaps in managing the safety risks that may occur. These gaps may occur when there is:
- a lack of understanding of how each person’s work will be carried out
- an assumption that someone else is managing the safety of the activity.
You should consider utilising the Third Party Engagement Checklist - Template as part of your own SMS to assist in clearly identifying and recording third party interactions that may have an impact on your safety risk management and performance. In addition, the Third Party Engagement Checklist - Template with instructions (DOCX, 157KB) is available for guidance on how you can reference the required template field information.
It is good business practice to continuously assess the risks associated with third party interactions.
Now that you better understand the potential impacts of third parties to your safety risk management performance, you should circle back to your populated Risk Register. Formally update the Risk Register to ensure it encompasses any third party related safety risks to the business and include any new or amended risk controls and treatments as a result.
For example, a new treatment in the Risk Register may be an action for management to revise your current Safe and Secure Loading Procedure to include the expected roles and responsibilities of a third party. You may also record that the contractual arrangements between both organisations are to be amended by a certain time, to reflect a strict requirement by the third party to follow the amended loading procedure.
Step 9 - Continuous improvement and change management
Continuous improvement and change management are important ongoing processes that can assist in managing current and emerging safety risks in the business. It is often considered the difference between managing safety and leading safety.
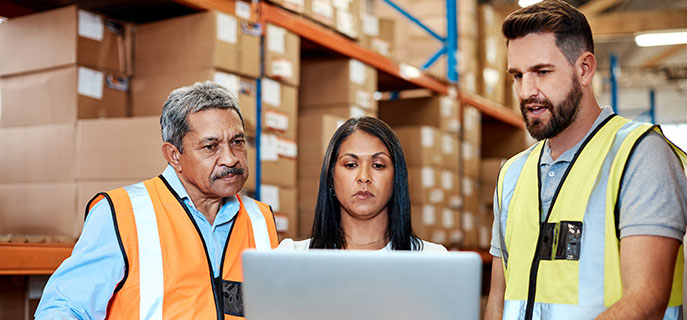
It is challenging for a business to consider where it can improve on its safety management and performance, if it has only recently developed and implemented the core or platform elements of its SMS.
The important focus at this stage of your journey is to ensure that all recommended processes and products described in the preceding steps of "Starting Out" (such as a populated Risk Register or Safety Training Calendar) have been embraced, developed, and implemented.
As previously described, you should ensure that any improvement actions associated with your current system and processes (such as need improvements arising from reported and investigated incidents) are documented and followed up via a Continuous Improvement Register - Template.
A stronger focus on continuous improvement starts with exercising safety leadership and integrating your SMS into normal business activities, rather than treating safety as a separate function. When a problem or incident occurs, it as an opportunity to learn and improve processes to prevent it happening again.
Continuous improvement contributes to the ongoing identification and management of safety risks through the review of products, services and transport activities.
The Continuous Improvement - Quick Guide contains greater detail on how to approach continuous improvement within your business. It contains a phased implementation schedule to guide continuous improvement across all elements of your SMS.
It is important to encourage staff involvement in your continuous improvement planning and actions. Staff and line managers can help to identify and solve safety issues and possible improvements with their own or collective ideas and suggestions. This promotes and builds upon a positive safety culture; a precursor to improved safety performance.
All businesses can experience change at different times but being prepared and ready for change can make the difference. Change may be in response to business needs and opportunities, or as a result of continuous improvement.
As part of your business processes, consider any parts of the intended change that may result in some form of safety risk. For example, an expansion of the business to now also transport livestock will create new safety risks to your transport task, which will require related planning and risk management.
At this stage, your Risk Register should be updated to reflect what new risks may be introduced to the business as part of the intended change, as well as any required new risk controls or future treatments.
Once your SMS has been fully developed and is maturing in its implementation and performance, it will require ongoing or more targeted processes to provide continuous improvement and effective safety change management.
Continuous improvement at this level involves planning and undertaking more holistic audits or assessments of your SMS and its effectiveness. This is more than just determining if staff are following key safety risk controls – such as a safety procedure but looks more widely at critical parts of the SMS to determine if they are indeed working as designed. Required improvements to these SMS areas can then be agreed, recorded, and implemented.
You should also consider adopting the Continuous Improvement – Toolbox Talk as part of your own SMS. It is a useful reference for managers to discuss with staff the organisation’s approach to continuous improvement, why it is important, and how they can become involved.
It is important to understand that there can be a link between your planned operational changes and the safety of operations. The Change Management - Quick Guide explains this process in more detail.
Keeping all parties informed can help any change transition occur more smoothly and help minimise any safety impacts to transport activities as part of the change. This includes regular and genuine communications to staff, line management and affected third parties.