Safety risk management is important for businesses that use or engage heavy vehicles as part of their operations or undertake tasks or activities that impact the safety of a heavy vehicle.
What is safety risk management?
Safety risk management is the systematic process of identifying and assessing potential hazards, considering the likelihood and severity of harm that could result from those hazards, and taking steps to mitigate risks by implementing considered strategies, systems and processes.
Informal safety risk management happens all the time. Workers considering the task at hand, will look at possible ways to complete the task, consider the things that might go wrong and then decide the best way to complete the task with the lowest chance of something going wrong. This could include seeking assistance from another worker, using a specific tool, wearing protective equipment or moving other people out of the way. This everyday process is basic safety risk management.
The purpose of this document is to outline a process that can be systematically applied to managing safety hazards and risks associated with your transport activities. Having effective processes in place helps to ensure the safety of all workers and the public, protects road and other infrastructure, prevents harm to the environment and prevents damage to heavy vehicles and loads.
Why is safety risk management important?
Safety risk management is a fundamental part of ensuring safety. There are inherent safety hazards and risks associated with the use of heavy vehicles which could result in serious injury or death. Identifying and understanding hazards and risks is crucial to preventing harm by reducing the likelihood and severity of incidents.
In addition to keeping workers, drivers and the public safe effective safety risk management can also assist in preventing potential financial loss. Financial losses are inevitable when incidents occur, no matter how large or small. For example, operational disruptions, damage to equipment, workers compensation, and costs of legal proceedings.
Good safety risk management practices result in positive safety outcomes and can also make your business a partner and employer of choice.
Safety risk management and the HVNL
This is an obligation to eliminate or minimise public risks, and a prohibition against directly or indirectly causing or encouraging a driver or another person, including a party in the CoR, to contravene the HVNL.
More information can be found in primary duty
What are public risks?
The HVNL defines 'public risks' in broad terms. Section 5 of the HVNL outlines the following:
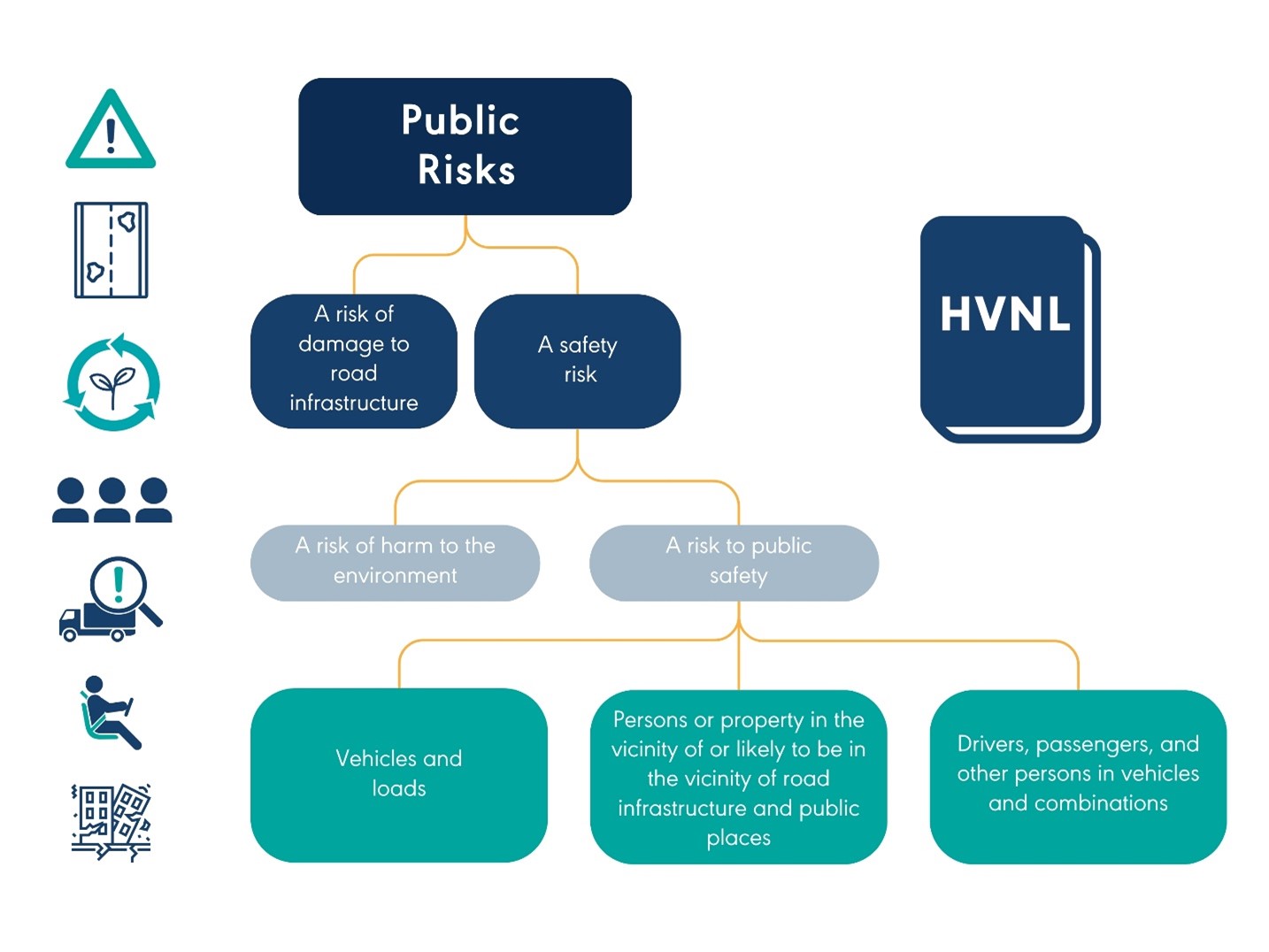
What are the legal requirements under 26C?
If your business is a party in the CoR and it fails to eliminate or minimise public risks so far as is reasonably practicable, then it may be in breach of its primary duty. It is important to understand that the primary duty is based on a positive duty to ensure safety. This means failing to control a risk is a primary duty breach even if no incident or crash occurs.
Do I have to do more to comply with the HVNL primary duty than WHS obligations?
The vast majority of the transport industry are confident and well informed in their understanding of how to manage their obligations under WHS and remain safe and compliant. A lot of the work you currently do to manage safety at your workplace as part of your WHS responsibilities will contribute significantly to complying with the HVNL primary duty. However, you need to think about what happens after a heavy vehicle leaves your premises and how your actions or inactions could impact other parties in the supply chain. For example:
- Failing to properly restrain a load on a heavy vehicle can impact the safety of others once the vehicle has departed.
- Failing to consider the heavy vehicle driver’s fitness for the duration of their shift could mean that their fitness to work deteriorates throughout the journey.
- Scheduling time slots that don’t allow for potential delays may put pressure on the driver to speed or skip or shorten rest breaks to make up for delays.
Compliance with the primary duty can be approached in the same way as the primary duty of care under WHS law and other duty-based offences. The standard is the same, to do what is reasonably practicable, but under the HVNL the duty holder must ensure safety beyond their premises and consider how to manage risks across all parts of the heavy vehicle journey they can control or influence.
So far as is reasonably practicable
So far as is reasonably practicable means an action that can reasonably be done in relation to the duty, considering relevant matters such as:
- the likelihood of a safety risk or damage to road infrastructure
- the harm that could result from the risk or damage
- what the person knows, or ought reasonably to know, about the risk or damage
- what the person knows, or ought reasonably to know, about the ways of removing or minimising the risk, or preventing or minimising the damage
- the availability and suitability of those ways
- the cost associated with the available ways, including whether the cost is grossly disproportionate to the likelihood of the risk or damage.
More information on reasonably practicable can be found in Regulatory Advice – Reasonably practicable.
Safety risk management
Safety risk management involves:
- identifying hazards associated with transport activities
- assessing the risks associated with hazards
- identifying and implementing control measures to eliminate or minimise risks
- reviewing the effectiveness of control measures, periodically and/or post any incident, to ensure they remain effective.
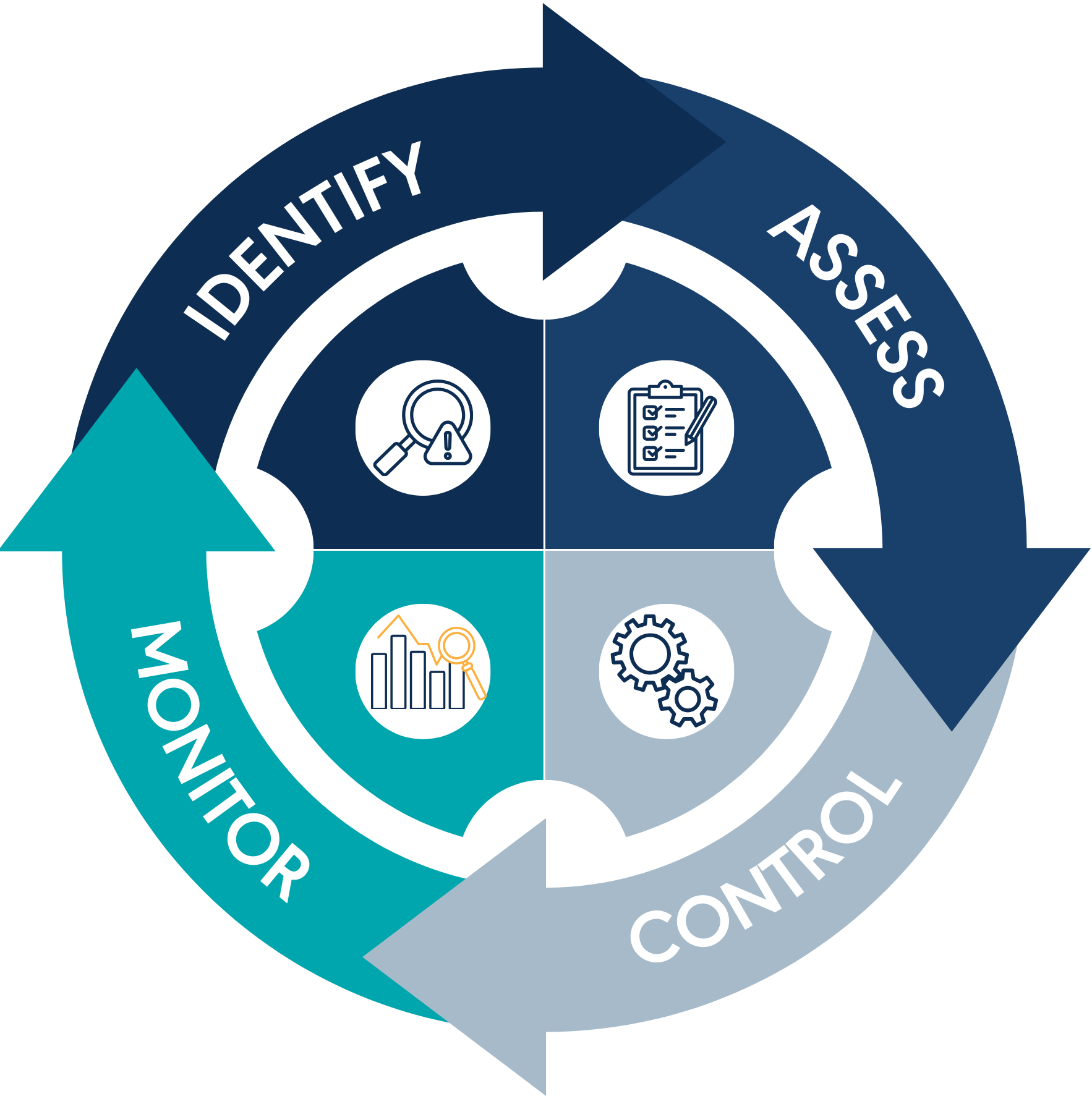
Identifying hazards
A hazard is a source of risk that has the potential to cause harm to a person or the environment, or damage to road or other infrastructure, heavy vehicles or loads.
Hazards can be categorised as different types including:
- Physical - vehicle collisions, pedestrians being struck by a heavy vehicle or moving plant, individuals or loads falling from vehicles, manual tasks, and vehicle noise and vibration.
- Biological - contact with animals, livestock effluent, contaminated soil and medical or other waste products.
- Chemical - dangerous goods for example petroleum products or exposure to exhaust emissions. Exposure to dangerous goods can harm persons within the vicinity of the heavy vehicle, the environment, and cause damage to infrastructure.
- Psychological - exposure to traumatic events, fatigue, distraction, stress, time pressures and extended work hours.
- Operational - heavy vehicle risks such as driver distraction, driving behaviour, situational awareness, risk appetite, adapting to changing conditions and mechanical failures.
Note: Multiple hazards can originate from the same source.
Hazard identification can be both planned and unplanned. Planned hazard identification may include:
- workplace inspections
- audits
- checklists such as daily pre-start inspection checklist
- incident investigations
- work or project planning
- communication and consultation activities such as toolbox talks.
Unplanned hazard identification may include:
- informal observations
- hazard reports
- complaints.
Safety hazards and risks associated with the use of heavy vehicles are well documented. It is your responsibility as a business to understand the safety hazards and risks associated with the operations and transport activities you undertake and invest in appropriate controls to mitigate these safety risks. Ensuring you remain up to date with industry standards and good practice is an excellent way to keep informed of relevant safety risks and controls. This can be done through a range of methods including:
- speaking with others in your industry sector
- subscriptions to publications relevant to your business
- referencing industry codes of practice
- advice and educational materials published by suitable authorities, for example, the NHVR, relevant industry bodies and other statutory authorities.
Assessing safety risks
Assessing safety risks is the process of considering the potential for harm to persons or property arising from identified hazards. Assessing your safety risks helps determine the probability of an incident occurring and the severity of its potential consequences. To evaluate a hazard’s risk, you should consider how, where, how much, and how long individuals are typically exposed to a potential hazard.
Risk assessments may also incorporate an evaluation against standards set by legislation, codes of practice and other industry benchmarks. Risk assessments should be undertaken by a competent person and in collaboration with relevant workers, stakeholders, and subject matter experts. Assessments should take into consideration known information about hazards, records of incidents, and previous or potential harm that may arise.
Risk assessments should be undertaken periodically, documented, and regularly reviewed. Assessment outcomes should be made available to all relevant parties.
More information on carrying out risk assessments can be found in SMS resources.
Controlling safety risks
When controlling safety risks your business should always begin by trying to eliminate risks. It may not be possible to eliminate or suitably mitigate a risk using a single control. In many cases a combination of controls may be needed to control the risk. Risks should be prioritised focusing first on the most significant risks, ensuring that the most dangerous hazards are addressed. This approach maximizes safety and efficiency by allocating resources and efforts where they are needed most, reducing the likelihood of severe incidents.
Safety risks can be minimised by implementing control measures such as:
- Substituting the high-risk activity with a lower-risk alternative. For example, scheduling work during daytime hours rather than at night to minimise the risks associated with fatigue.
- Isolating the high-risk activity so that no persons are exposed to the risk. For example, establishing exclusion zones in loading and unloading areas to minimise interactions between individuals and the risk.
- Implementing engineering controls that reduce the likelihood of a risk occurring or the severity of harm that could occur. For example, provide lifting aids when manual tasks such as loading or unloading are being performed.
- Using administrative interventions such as providing training about hazards and risks so that workers are aware of the safety risks and controls.
- Using personal protective equipment such as high-visibility clothing, gloves or safety shoes.
Hierarchy of controls
Businesses may also consider adopting a ‘hierarchy of controls’ approach for specific risks to systematically minimise the likelihood of incidents occurring. The key principle is to prioritise higher-level controls, which are more effective and less dependent on human performance, while recognising that administrative controls and the use of personal protective equipment should only be relied upon when absolutely necessary, or as a last line of defence.
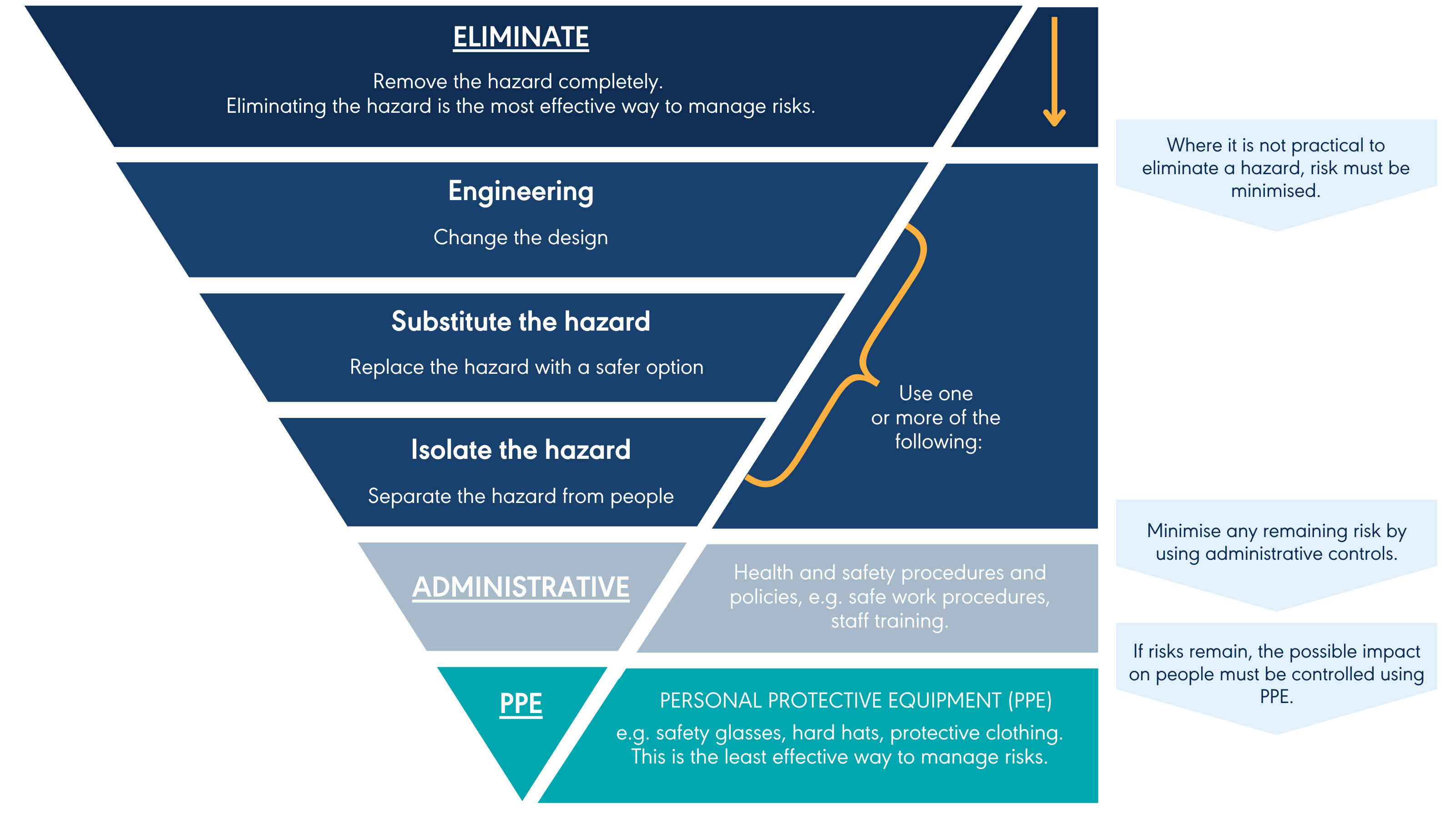
Safety risk registers
Recording safety risks is crucial for ongoing control and monitoring. Safety risk registers provide a valuable resource when performing safety risk management activities such as risk assessments or incident investigations and provide a means to:
- monitor safety risks and controls
- allocate and manage resources appropriately
- provide information about risks and their controls to workers and other stakeholders
- periodically review risks and the effectiveness of risk controls in consultation with workers and other stakeholders.
Monitoring and reviewing safety risks and controls
Control measures should be regularly reviewed to ensure that they are being correctly applied and remain effective. Control measures should be reviewed:
- when a new hazard or risk is identified, or a new transport activity is commenced
- when measures are not effective in controlling the risk (e.g. following an incident)
- when you are unsure how to best control the risk or there is uncertainty about how a hazard may result in harm or loss
- following results of a consultation that indicates a review is necessary
- if a safety representative requests a review
- following an inspection or audit finding
- when a change is proposed to the task or equipment that presents the hazard or risk
- when changes occur that may impact on the effectiveness of existing controls
- periodically, annually at a minimum.
Maintaining records
It is important to document safety risk management processes to demonstrate what has been done to manage risks. Maintaining accurate records helps when monitoring controls and reviewing risks to understand how risks were controlled and why, and to record any changes.
The type of records that should be maintained include:
- completed risk assessments
- hazard report forms
- Safety Risk Registers
- incident reports and investigation records
- worker medical assessments
- workplace assessments
- injury management and return to work plans
- training records.
When determining the type of records that must be maintained and relevant disposal periods, you should consult the records management retention requirements relevant to the state or territory where you are conducting your business operations and/or your transport activities. This means that you may have to meet requirements in multiple jurisdictions.
Additional resources to help you understand what to record and templates can be found in SMS resources.