Loading Guide – Intermediate Bulk Containers (IBCs)
Loading Guide – Intermediate Bulk Containers (IBCs)
National
Heavy
Vehicle
Regulator
This guide is part of a series of loading guides that provide tips and tricks to help you understand good load restraint. More detailed information on the principles covered by this guide can be found on page 125 of the Load Restraint Guide 2025.
What are IBCs?
Intermediate bulk containers (IBCs) are industrial grade reusable containers engineered for the mass handling, transport, and storage of liquids, semi-solids, pastes, or solids.
They can be made of metal, plastic, or composite of materials.
There are three main components of an IBC:
- the container, which is made of different plastic’s depending on use
- the pallet mounted base, which is made of galvanised steel or plastic
- the protective cage, which is made of galvanised steel tubes or a wire cage.
How much do they weigh?
The weight of an IBC can vary greatly, depending on the construction of the IBC and the material that is carried.
For example, an empty IBCs can weigh around 65kg for a steel base or around 52kg for a plastic base.
If filled with 1100 litres of AdBlue, the complete IBC weighs around 1270kgs, but if filled with Chlorine, the IBC weighs around 1785kgs. It is important to know the correct weight of your load to enable you to calculate the number of restraints required to ensure it is sufficiently restrained.
Examples using different friction surfaces
The below restraint requirements have been calculated using the tables on page 274 and 275 of the Load Restraint Guide.
Steel on steel – very low friction 0.2
11 webbing straps
High risk. Do Not Continue – Not Safe
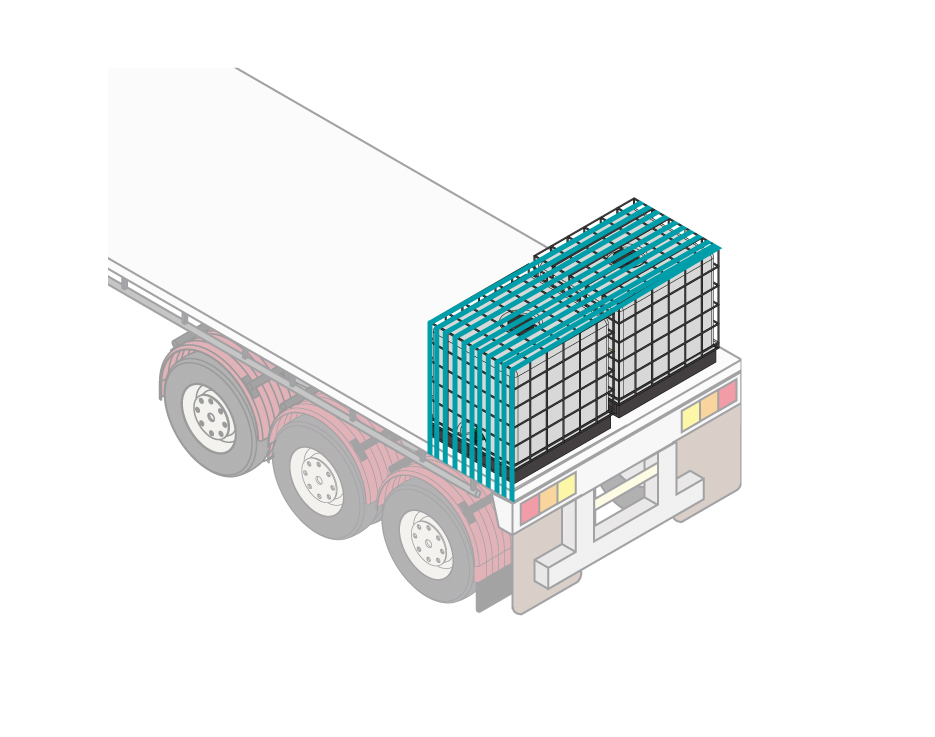
Steel on timber – medium friction 0.4
4 webbing straps
Medium risk
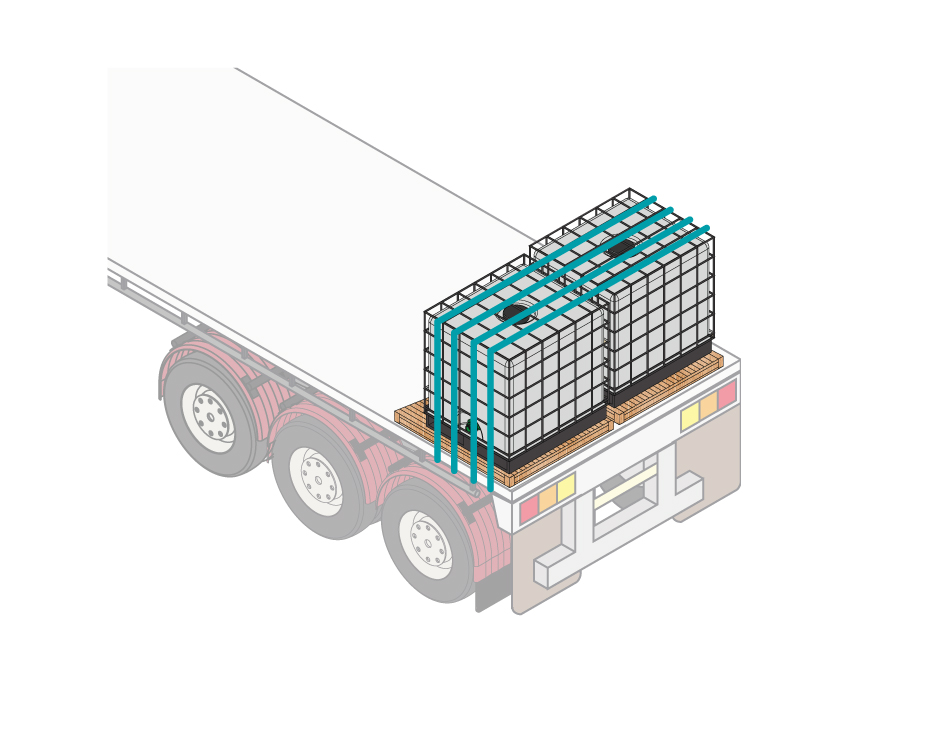
Steel on rubber load mat – high friction 0.6
2 webbing straps
Low risk
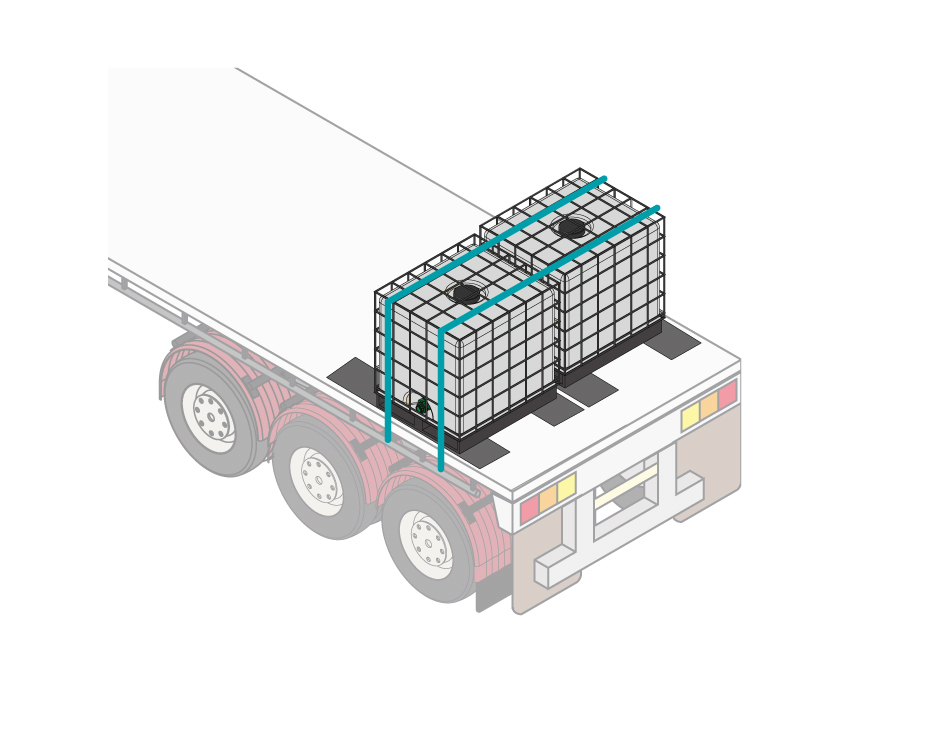
Steel on rubber load mat – blocked.
1 webbing strap
Very low risk
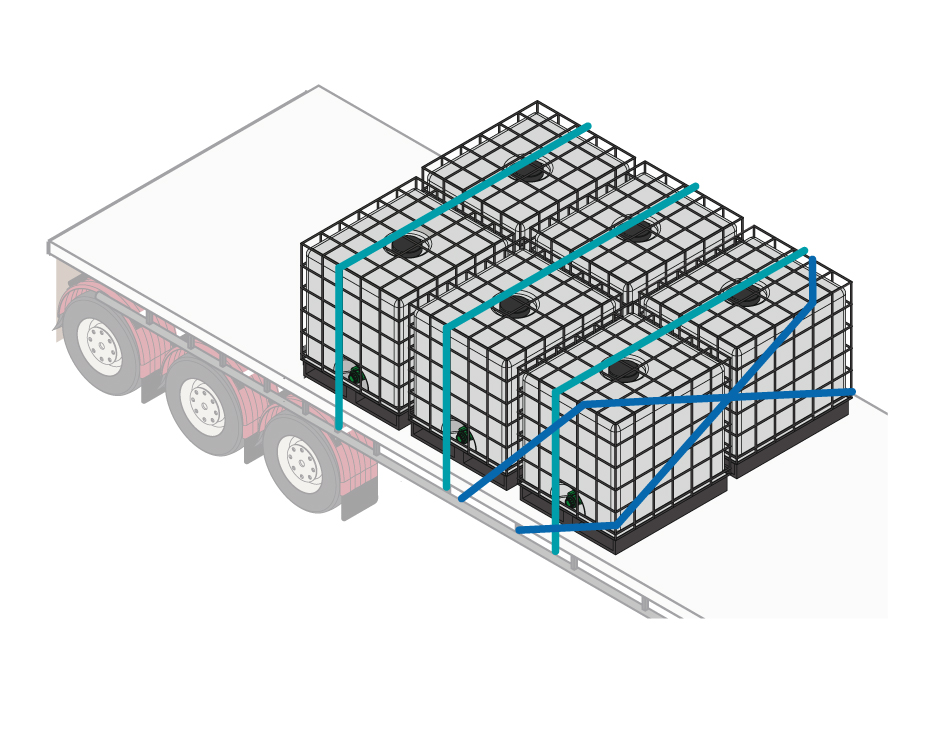
IBCs placed directly on a steel deck and not blocked require multiple lashings and may crush the frames. The amount of restraint required to ensure safety is excessive and impractical.
Note: The NHVR strongly recommends where the coefficient of friction is very low or low (below 0.3) and the load is not blocked, safe loading practices must incorporate a friction medium, such as timber dunnage, timber pallets, or load mat to increase the coefficient of friction.
Tips
Understanding how the load may behave during transport will ensure your restraint system is appropriately rated.
Where possible block against a headboard or use packing to provide the blocking. The use of non-rated headboards or gates is not advised.
Risks
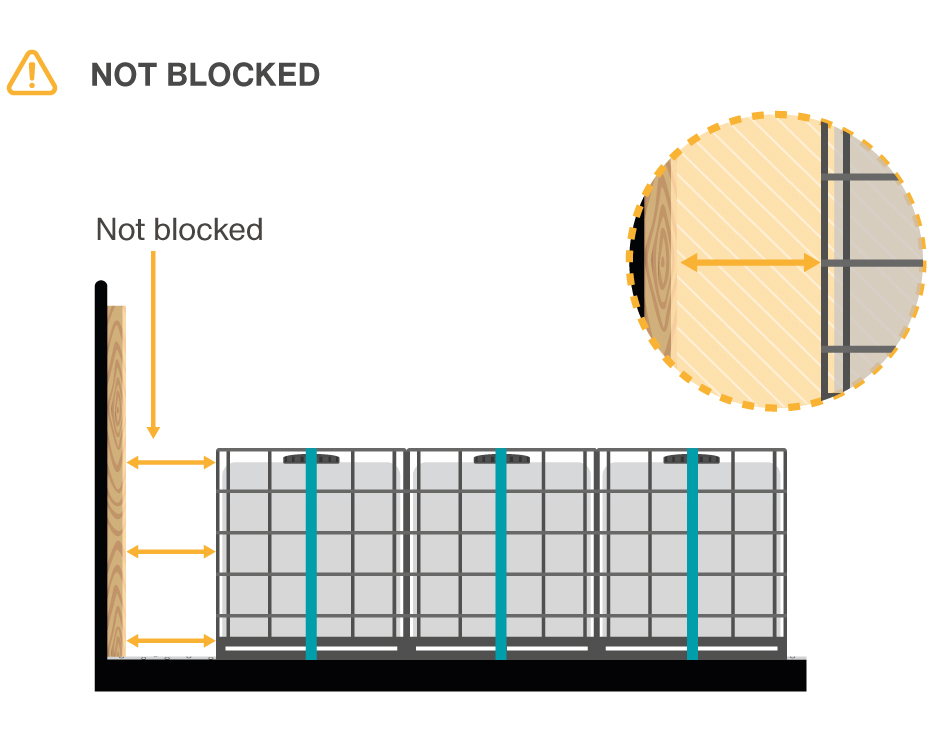
Good practice
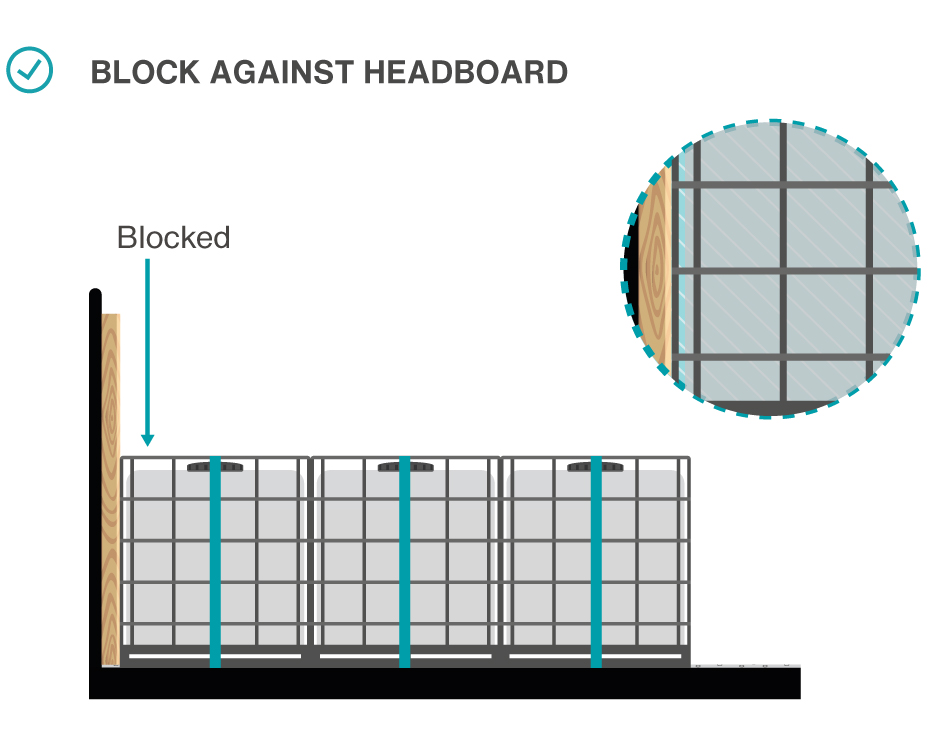
Liquid slosh and surge in partially filled IBCs can affect the vehicles stability and will add pressure on the load restraint system. Where possible fill IBCs completely or to the fill line. This will reduce slosh and surging as much as possible.
Risks
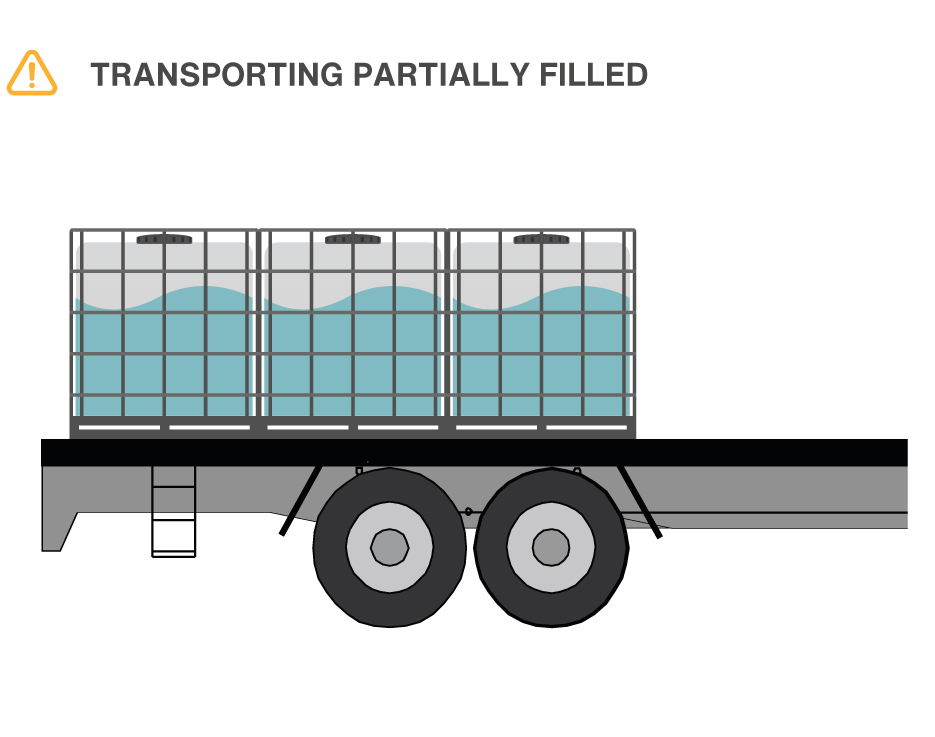
Good practice
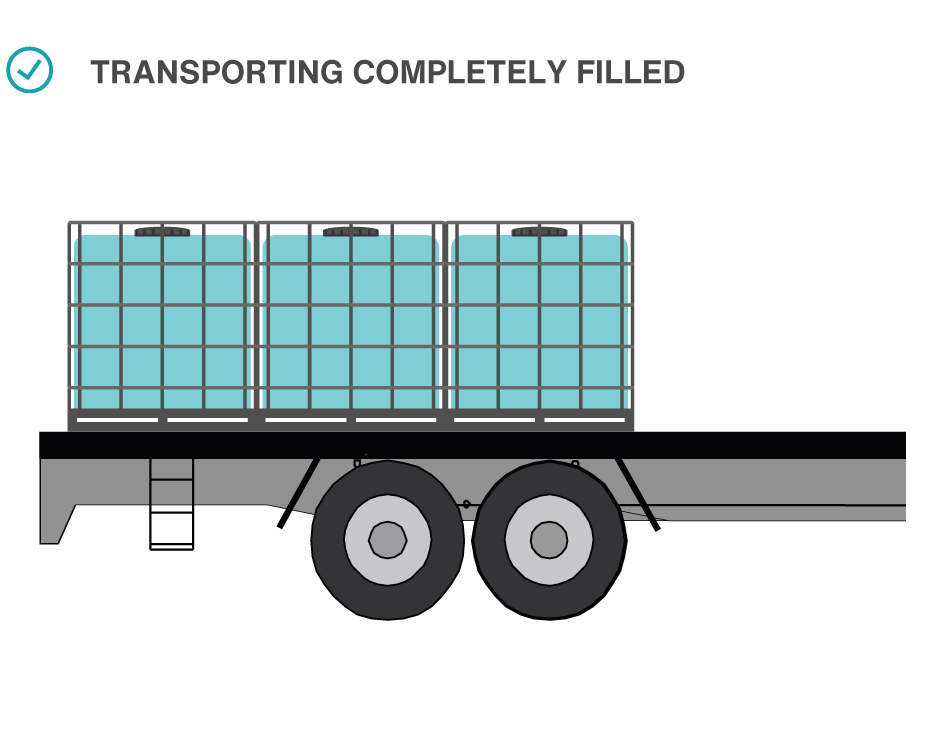
Where a suitably engineered blocking structure is not available, use crossover straps to block the load at the front. Loads that are blocked require less lashings to meet the performance standards and loading requirements.
Risks
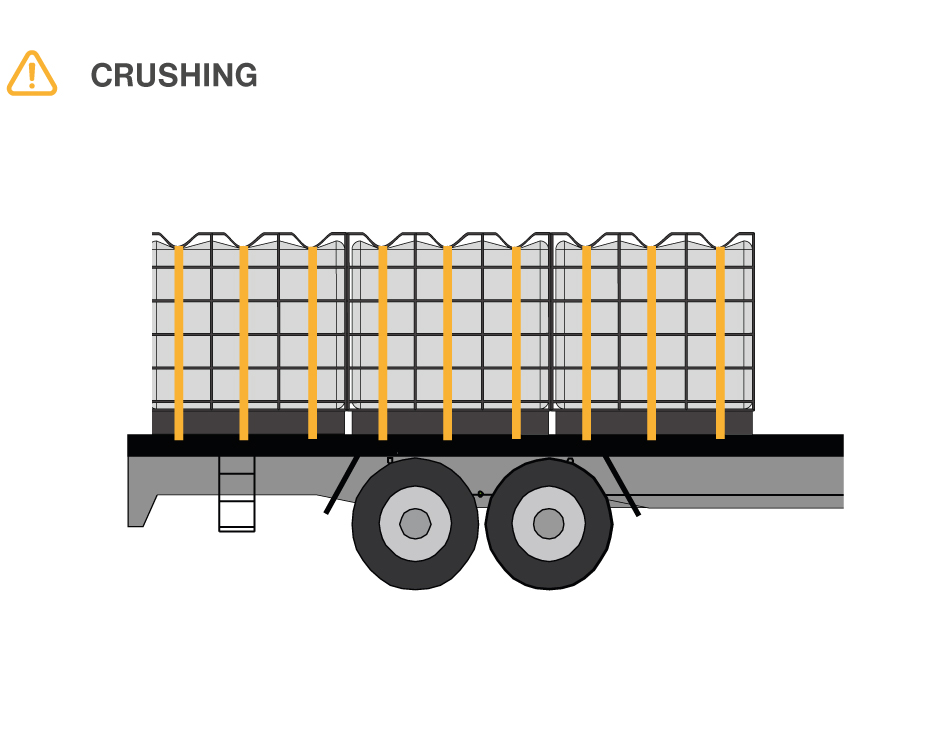
Good practice
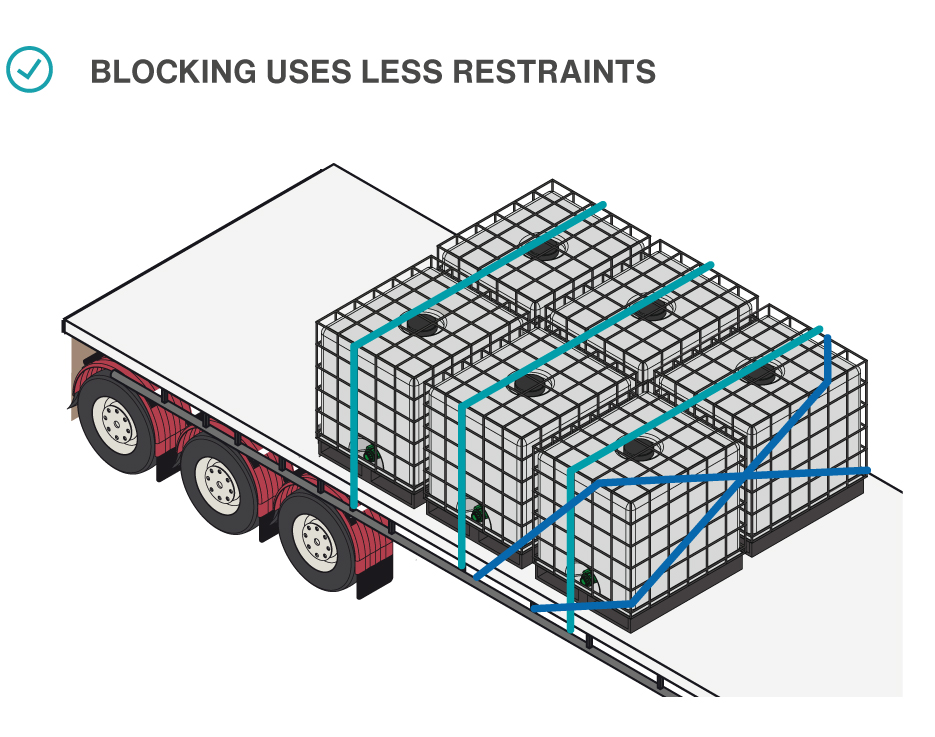
Steel or plastic framed IBCs on steel loading decks have very low friction and require multiple lashings to restrain the load. Place IBCs with low friction bases on timber or rubber load mat to improve the coefficient of friction.
Risks
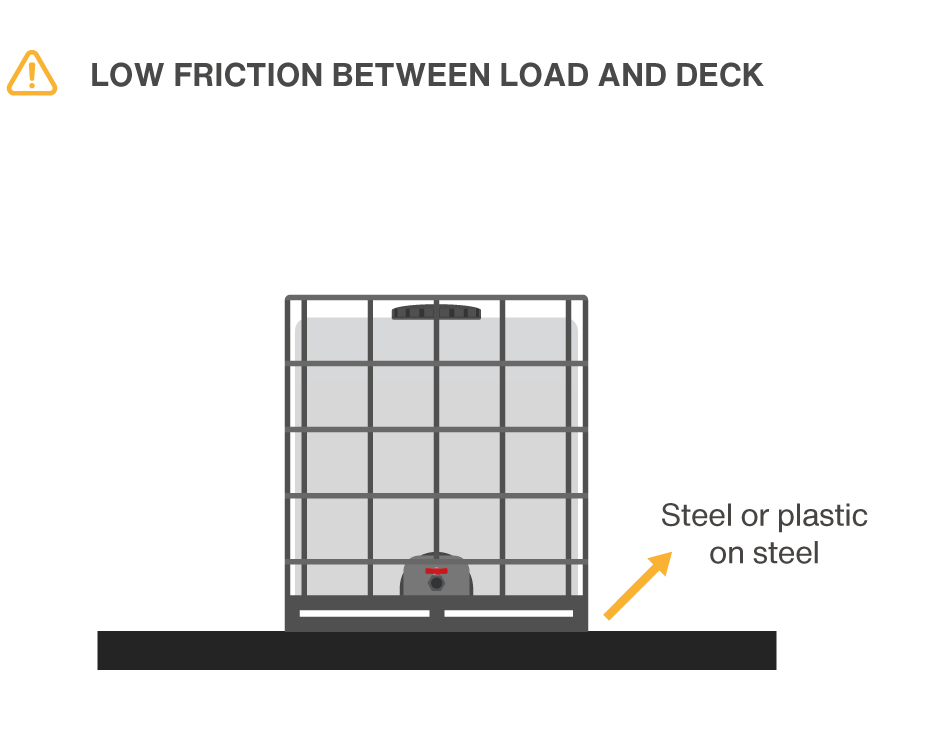
Good practice
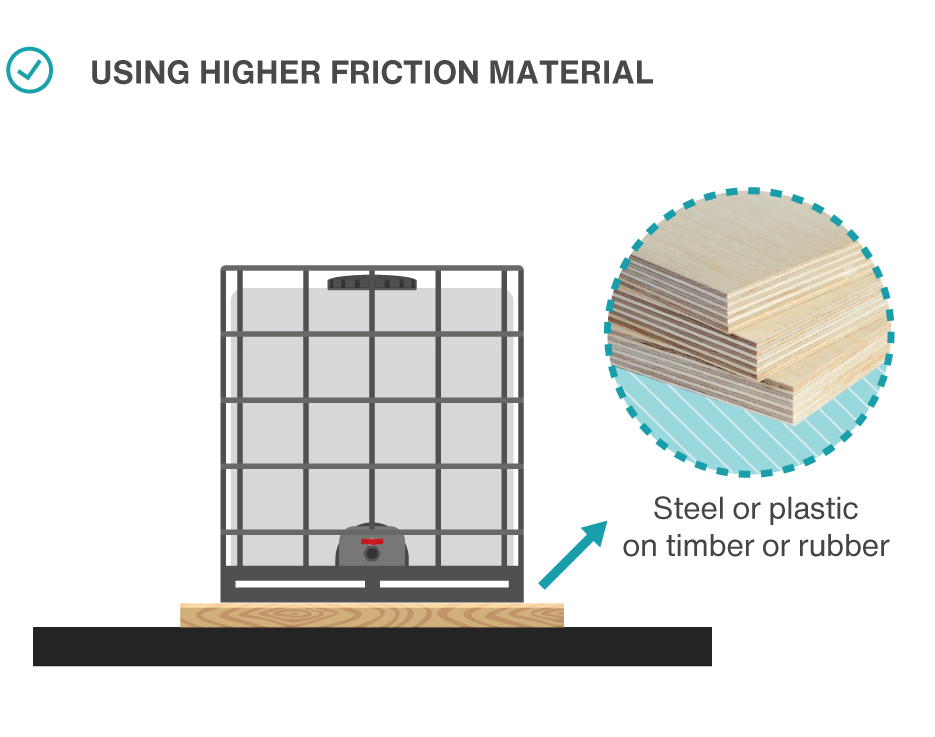
Case study
This is a common example of a restraint system used for IBCs.
If any of these IBCs were to shift or fall during transport, they could cause serious injury or death to other road users or damage to road infrastructure. If they were filled with hazardous chemicals this could be an environmental disaster.
In this example a step deck trailer is loaded with 2x7 rows of IBCs on the lower deck and 2x3 rows of IBCs on the top deck. The loading decks on the trailer are completely full, no gaps.
The IBCs are filled with water and weigh 1000kg. The steel framed IBCs are sitting on a steel deck which has a very low static friction (0.2). The push-up type 50mm webbing ratchet is capable of a pre-tension of around 300kgf.
In the image you can see the frame of the IBC is already bending at the top with just one strap over the cage.
Applying the tables on page 249 of the Load Restraint Guide, 6 straps per row are required due to the very low friction between the IBC and the deck (steel on steel).