Loading Guide - Stretch and Shrink Wrapping
Loading Guide - Stretch and Shrink Wrapping
National
Heavy
Vehicle
Regulator
This guide is part of a series of loading guides that provide tips and tricks to help you understand good load restraint. More detailed information on the principles covered by this guide can be found on page 35 of the Load Restraint Guide 2025.
What is stretch and shrink wrapping?
Stretch wrapping is a stretchable plastic film that is wrapped around smaller/individual items, with tension, to unitise (hold together) a load on a pallet.
Shrink wrapping is also a plastic film that is wrapped around small items to unitise the load but shrinks to increase the tension/clamping effect when a heat source is applied to the film.
Both can be manufactured in different thicknesses, colours and sizes depending on the application. Unless the capacity of the wrapping material is known, its use should not be considered in the calculations when designing a load restraint system.
How to use
Manufacturers will have specific instructions on how to use their products. Stretch or shrink wrapping, on its own, is not suitable for restraining heavier loads or loads with edges or corners that can tear or penetrate wrapping.
The number of wrappings required depends on the weight of the goods and the friction levels between the layers of product and the pallet. Stretch or shrink wrapping can be applied manually by hand or mechanically by a machine. It is important to make sure you wrap around the pallet at the base to unitise the load to the pallet.
Rating and certification
Some manufacturers provide load ratings and certification for their products.
The load restraint guide provides guidance based on some best practice restraint approaches that have known values etc.
It’s not possible to factor shrink wrapping because its restraint performance is too variable. If you wish to include shrink wrapping in your load restraint system, then verification and testing is the best way to ensure a product is appropriate and compliant.
Tips
Follow all manufacturer’s instructions for the use of stretch and shrink wrapping.
Low friction between rows can cause excessive movement. Applying anti-slip material between rows can help control movement.
Risks
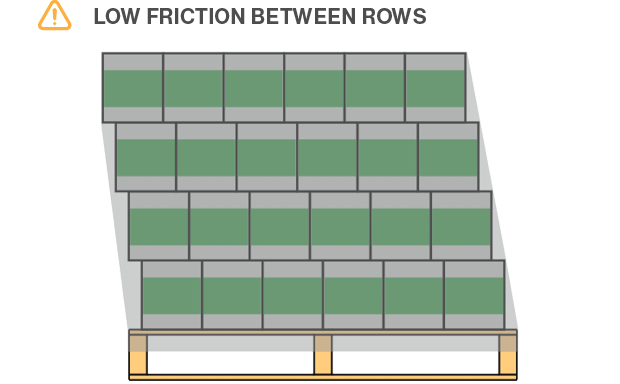
Good practice
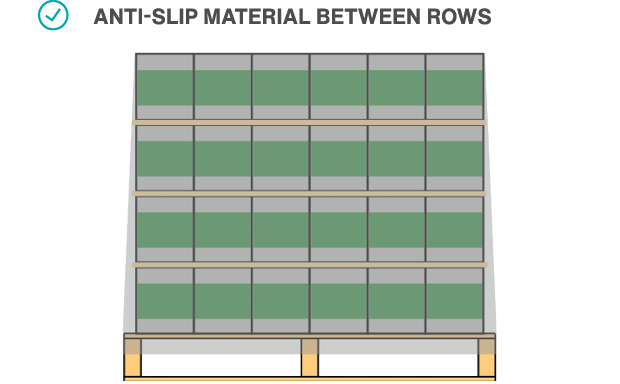
The load is not unitised (held together) and not fit for transport. A combination of extra restraints and shrink wrap ensures the load is unitised and safe for transport.
Risks
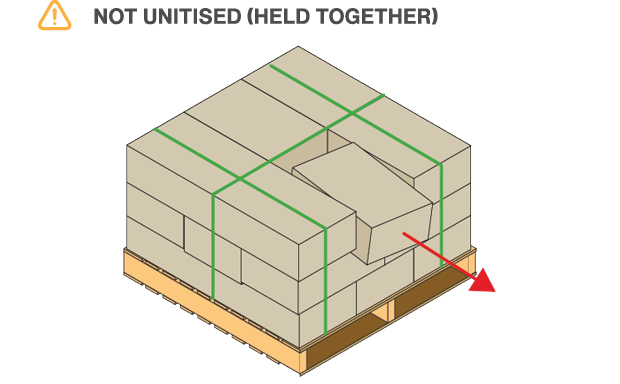
Good practice
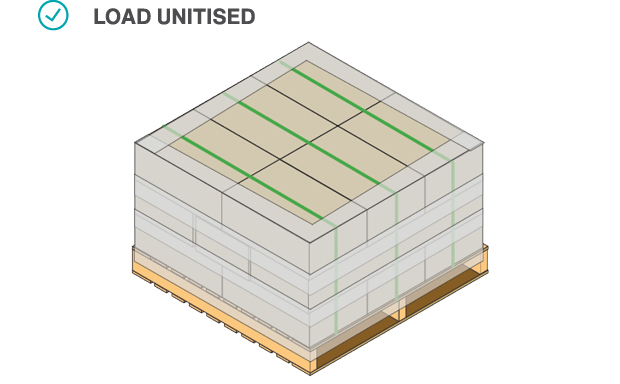
Shrink wrap may be suitable for light loads, however heavy loads will require additional restraint.
Risks
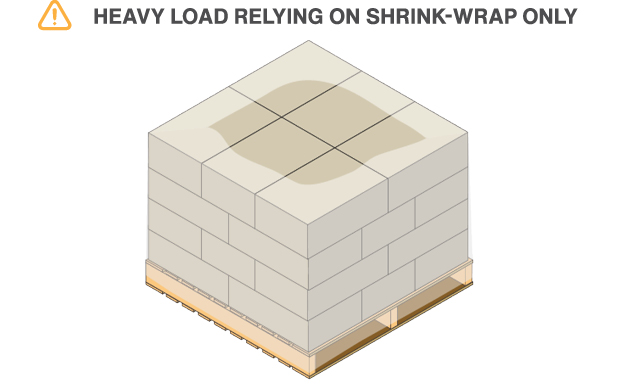
Good practice
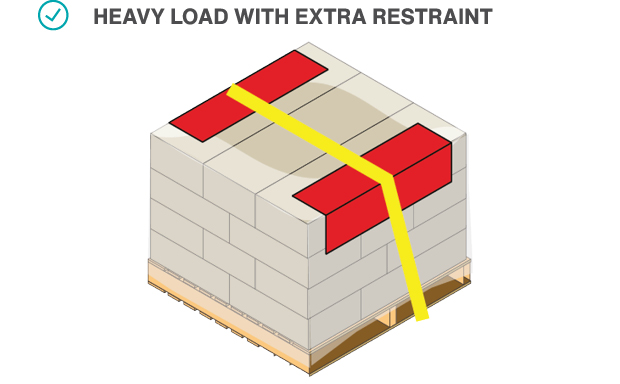
Case study
This is an example where wrapping was relied upon for restraining the load to the pallet. This load probably appeared to be appropriately wrapped when it was first applied in the factory but now is starting to fall apart and failed during transport.
While some of the load restraint principles applied in this guide have been used, there are some issues that pose loading risks:
- Sharp and rigid edges on the bricks have damaged the wrap and caused it to come away from the load.
- There are also signs of other damage to the wrap that has seen it ride up and expose layers of bricks. These have led to bricks starting to come out of the packs in just a short time after leaving the yard.
- The edge protection used at the top of the load does very little to spread the force provided by the webbing strap. The force from the webbing strap would only be acting on the very middle of the pack.
Basically, the only thing holding these bricks in place is the strength in the plastic wrapping.
If a brick was to become dislodged from the vehicle whilst travelling at a moderate speed of 60 km/h, the consequences to other road users could be catastrophic.